Cen-tia-g-lithium-ion-battery-manuf-application-note-b210915en-b.pdf

/ APPLICATION NOTE
Monitoring Water Vapor in the Lithium-ion
Battery Manufacturing Process
The lithium-ion battery manufacturing process is sensitive to moisture. This challenging production environment demands a water vapor detection instrument with reliable performance and strong resistance to process byproducts that may be present in the atmosphere.
Dry-air management is essential
environment must be controlled
resolution and accuracy necessary
during the lithium-ion (Li-ion) battery
to preserve optimum production
for meaningful measurement at
manufacturing process for three
conditions. The typical dew point
this level. For example, when the
reasons: first, to prevent unwanted
temperature range of the processing
dew point temperature is -50 °C,
chemical reactions that can cause
environment is from -50 °C to -40 °C.
a 5 °C rise to -45 °C represents a
hazards such as fires and explosions;
Dew point is used to express water
corresponding relative humidity
second, to prevent product quality
vapor concentration at this level
change of only 0.1% – a value that is
problems; third, to understand and
because the corresponding relative
difficult to distinguish from noise.
control costs associated with drying
humidity value is less than 1%. Most
(Visit Vaisala's knowledge center and
large volumes of air. Lithium-ion
instruments used for measuring
use or download our free humidity
battery manufacturing processes
relative humidity, even if they
are carried out in dry rooms or
convert the display and output values
glove boxes where the local micro-
to dew point temperature, lack the

Optimal location for
Solutions for dew point measurement
dew point sensors Dew point instruments can be used
Common solutions for dew point
Aluminum oxide and silicon oxide
in a variety of ways to achieve the
measurement include chilled mirror
sensors can measure extremely low
objectives outlined above. The
hygrometers, oxidized aluminum
dew point temperatures. Care should
actual air dryer can be monitored
or silicon sensors, and polymer
be taken to monitor the calibration
and controlled using dew point
moisture sensors. Each has strengths
of these devices, as any gas that
measurement. In some cases, dryer
contributes to continuing oxidation of
performance can be improved and
The chilled mirror hygrometer
the sensor itself will cause a drift in
energy consumption reduced by
uses optical reflection to detect
implementing dew point demand
the condensation temperature on
Polymer sensors can be formulated
switching. Dew point instruments
a reflective surface (the mirror).
to resist a wide variety of chemical
can also be installed at the inlet of
These devices are very accurate in
contaminants. Unfortunately, most
each process on the supply gas line,
laboratory conditions, but subject
polymer sensors function exclusively
either directly or by using a sampling
to measurement error known as
in the percent relative humidity range
cell or ball valve. These instruments
the Raoult effect when the sample
and are therefore not suitable for use
can detect problems quickly and
gas contains solvents that go into
when the relevant dew point values
help determine whether the problem
solution with the condensate on the
are below -20 °C.
is localized or more general. Finally,
mirror. Strong acids or bases may
dew point instruments can be
also damage the mirror surface.
installed in the general work area and used as environmental monitors.
Contamination issues
Vaisala solution for dew point measurements
Dew point sensors can be
in Li-ion battery manufacturing
contaminated in the production
Vaisala offers a chemically resistant,
the sensor briefly and observing
environment by chemicals that
high-polymer dew point sensor that
the change in measured relative
evaporate from electrolytes used
is actively manipulated to achieve
humidity, which is physically related
in the process. Liquid electrolytes
long-term reliability with very little
to temperature. If the change is
in a typical lithium-ion battery may
measurement drift.
not as expected, the algorithm
consist of lithium salts such as LiPF6,
The Vaisala DRYCAP® sensor uses
corrects the sensitivity of the sensor,
LiBF4, or LiClO4 in an organic solvent
auto-calibration to monitor sensor
thereby maintaining accuracy in dry
– usually ethylene carbonate (EC),
accuracy and any necessary
measurement conditions, where it is
dimethyl carbonate (DMC), or Methyl
adjustments. The auto-calibration
Ethyl Carbonate (MEC). All of these
procedure is based on heating
solvents have the potential to damage a dew point sensor. If the electrolyte is LiPF6, it is present as Li+ and PF6- ions. Reaction with H2O in the environment will create hydrofluoric
(HF) acid. This is a strong acid that
Thin-film polymer
erodes the isolator film between the
battery terminals, increasing the risk
of short circuit and fire. It can also degrade the dew point sensor. The
challenges are similar for different battery formulations.

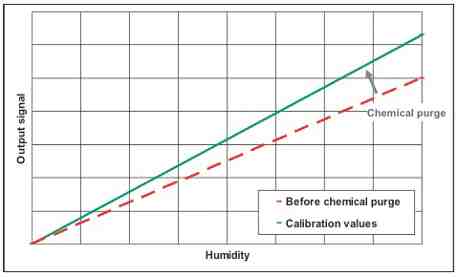
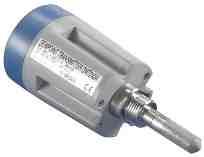
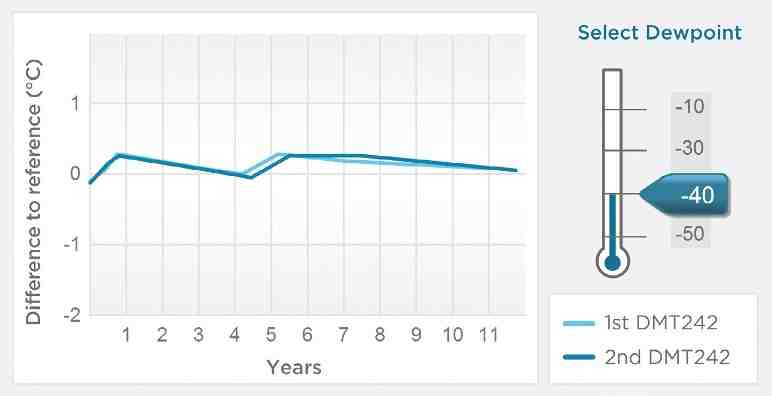
Another vital feature of the DRYCAP® sensor is the purge function. In Li-ion manufacturing,
The purge function
the demanding chemical conditions
briefly heats the
cause diffusion of contaminants,
sensor in order to
mainly hydrocarbons from the
remove any volatile
used solvents, into the sensor
contaminants from
polymer. Sensor contamination may result in an irreversible change in
the polymer.
sensitivity, which eventually cannot be compensated for by calibration and leads to sensor malfunction.
Contaminants may decrease the sensor sensitivity over time. Vaisala DRYCAP®
The purge function briefly heats the
sensor has automatic purge function which restores the sensor performance by
sensor in order to remove any volatile
evaporating impurities away from the sensor element.
contaminants from the polymer. The function can be initiated manually or
options for Li-ion battery
various options and accessories,
automatically, and the purge interval
manufacturing related measurements,
all with different options for output
can be adjusted to suit the operating
with products ranging from small,
and mounting. Compatibility with
compact transmitters perfect for
handheld devices allows for easy
The Vaisala dew point measurement
equipment manufacturers to rugged
on-site spot-checking and calibration
product family includes several
industrial field instruments with
Recommended products
DMT242 Transmitter for Industrial Dryer Applications
-60. +60 °C (-76.+140 °F) Td with ±2 °C (±3.6 °F) accuracy
• Sensor options for desiccant and refrigeration dryers• Pressure up to 20 bar• DRYCAP® sensor technologyRead more or download the datasheet a
The graphs above are derived from an ongoing test in which two Vaisala DRYCAP®
DMT242 dewpoint transmitters were installed in a compressed air line ca 11 years
ago and have not been recalibrated or adjusted. The line conditions are representative
of instrument air. The x-axis represents years, the y-axis represents difference to the
reference value at periodic checks.

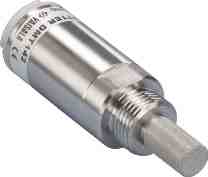
Hand-Held DM70 Meter for Spot-Checking and Field Calibration-60. +60 °C (-76.+140 °F) Td with ±2 °C (±3.6 °F) accuracy• Fast response – just minutes• Easy-to-use • Multilingual menu (EN, CN, DE, FI, FR, JP, RU, SE, SP)• Data logging and transfer to a PC via MI70 Link software• Compatible with DMT132, DPT146, DMT143, DMT242, DMT152, DMT340 • DRYCAP® sensor technologyRead more a
Configurable Fixed Mount DMT340 Transmitters-60. +45 °C (-76. +113 °F) Td with ±2 °C (±3.6 °F) accuracyConfigurable with various options • Display/keypad • Data logging and Relay module • Multiple probe option• Integrated data logging with over four years of measured history • Multilingual menu (EN, CN, DE, FI, FR, JP, RU, SE, SP)• Pressure up to 50 bar• DRYCAP® sensor technologyRead more
DMT143 Miniature Dew Point Transmitter
-60. +60 °C (-76. +140 °F) T with ±2 °C (±3.6 °F) accuracy
• Small size for compact industrial dryer applications• Stable and cost-efficient• LED alarm for exceeded dew point level• Pressure up to 50 bar• DRYCAP® sensor technologyRead more a
No single dew point sensor technology is suitable for all applications. However, Vaisala DRYCAP® technology has been tested and proven in a variety of applications, including dry-room monitoring, for more than ten years. Vaisala DRYCAP® instruments are available as low-cost transmitters or fully configurable field instruments. They are easy to install and use, and all models include probes with standard ISO or NPT threads. Vaisala sampling cells are available with threaded connections compatible with a wide variety of fittings, or with welded compression fittings to accommodate 6 mm or 1/4" tubing. A ball-valve installation allows the dew point probe to be installed in or removed from a process without process shutdown.
Contact Vaisala for expert guidance on dew point measurement and to find out more about Vaisala DRYCAP® instruments.
Ref. B210915EN-B Vaisala 2014
This material is subject to copyright protection, with all copyrights
retained by Vaisala and its individual partners. All rights reserved. Any logos and/or product names are trademarks of Vaisala or its individual partners. The reproduction, transfer, distribution or storage of information contained in this brochure in any form without the prior written consent of Vaisala is strictly prohibited. All specifications — technical included — are subject to change
Scan the code for more information
without notice.
Source: http://www.vaisala.de/Vaisala%20Documents/Application%20notes/CEN-TIA-G-Lithium-Ion-Battery-Manuf-App-note-B210915EN-B-LOW.pdf
bs_bs_banner Addiction Biology Chronic loss of noradrenergic tone producesβ-arrestin2-mediated cocaine hypersensitivity andalters cellular D2 responses in the nucleus accumbens Meriem Gaval-Cruz1*, Richard B. Goertz2*, Daniel J. Puttick1, Dawn E. Bowles3,Rebecca C. Meyer4, Randy A. Hall4, Daijin Ko5, Carlos A. Paladini2 & David Weinshenker1
Impact of recipient ABH secretor status on outcome in minor ABO-incompatible hematopoietic stem cell transplantation Andreas Holbro,1,2 Martin Stern,1 Laura Infanti,1,2 Alix O'Meara,1 Beatrice Drexler,1 Beat M. Frey,3 Jean-Marie Tiercy,4 Jakob R. Passweg,1 Christoph Gassner,3 Andreas Buser,1,2 and Joerg-Peter Sigle2,5