Gcs.gov.sa
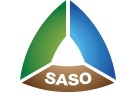
KINGDOM OF SAUDIA ARABIA
Saudi Standards, Metrology and Quality Org.(SASO)
Standard No.
Reference No.
Cement -- Test methods -- Part 2: Chemical analysis by X-ray
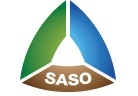
NATIONAL FOREWORD
The Saudi Standards, Metrology and Quality (SASO) has adopted without any technical changes the International Standard:
Issue Year
Cement -- Test methods -- Part 2: Chemical analysis by X-ray fluorescence
Cement — Test methods —
Part 2:
Chemical analysis by X-ray fluorescence
Ciments — Méthodes d'essais —
Partie 2: Analyse chimique par spectrométrie de fluorescence X
ISO 29581-2:2010(E)
ISO 29581-2:2010(E)
PDF disclaimer
This PDF file may contain embedded typefaces. In accordance with Adobe's licensing policy, this file may be printed or viewed but shall not be edited unless the typefaces which are embedded are licensed to and installed on the computer performing the editing. In downloading this file, parties accept therein the responsibility of not infringing Adobe's licensing policy. The ISO Central Secretariat accepts no liability in this area.
Adobe is a trademark of Adobe Systems Incorporated.
Details of the software products used to create this PDF file can be found in the General Info relative to the file; the PDF-creation parameters were optimized for printing. Every care has been taken to ensure that the file is suitable for use by ISO member bodies. In the unlikely event that a problem relating to it is found, please inform the Central Secretariat at the address given below.
COPYRIGHT PROTECTED DOCUMENT
ISO 2010 All rights reserved. Unless otherwise specified, no part of this publication may be reproduced or utilized in any form or by any means, electronic or mechanical, including photocopying and microfilm, without permission in writing from either ISO at the address below or ISO's member body in the country of the requester.
ISO copyright office Case postale 56 • CH-1211 Geneva 20
Tel. + 41 22 749 01 11 Fax + 41 22 749 09 47 E-mail copyright@iso.org Web www.iso.org
Published in Switzerland
ISO 2010 – All rights reserved
ISO 29581-2:2010(E)
Contents
ISO 2010 – All rights reserved
ISO 29581-2:2010(E)
Foreword
ISO (the International Organization for Standardization) is a worldwide federation of national standards bodies (ISO member bodies). The work of preparing International Standards is normally carried out through ISO technical committees. Each member body interested in a subject for which a technical committee has been established has the right to be represented on that committee. International organizations, governmental and non-governmental, in liaison with ISO, also take part in the work. ISO collaborates closely with the International Electrotechnical Commission (IEC) on all matters of electrotechnical standardization.
International Standards are drafted in accordance with the rules given in the ISO/IEC Directives, Part 2.
The main task of technical committees is to prepare International Standards. Draft International Standards adopted by the technical committees are circulated to the member bodies for voting. Publication as an International Standard requires approval by at least 75 % of the member bodies casting a vote.
Attention is drawn to the possibility that some of the elements of this document may be the subject of patent rights. ISO shall not be held responsible for identifying any or all such patent rights.
ISO 29581-2 was prepared by Technical Committee ISO/TC 74, Cement and lime.
ISO 29581 consists of the following parts, under the general title Cement — Test methods:
⎯ Part 1: Analysis by wet chemistry
⎯ Part 2: Chemical analysis by X-ray fluorescence
ISO 2010 – All rights reserved
ISO 29581-2:2010(E)
This part of ISO 29581 incorporates the following technical principles based on comments received by the Secretariat.
a) It provides an analytical method based on X-ray fluorescence (XRF) for use as the alternative method for
the analysis of cement. When correctly calibrated according to the specified procedures and reference materials, it provides a method of suitable precision for conformity and information purposes.
b) It introduces a reference method for TiO2, P2O5, SrO and Br analysis.
c) Traceability of the method relies upon reference materials and "pure" chemicals so that the ultimate
traceability to basic international chemical standards relies upon classical analytical methods that are outside of the scope of this part of ISO 29581.
XRF and other instrumental methods, such as differential thermal analysis for determination of carbon dioxide, atomic absorption spectroscopy, etc., can be used as alternative methods, provided they are calibrated against the reference methods, or against internationally accepted reference materials.
ISO 2010 – All rights reserved
INTERNATIONAL STANDARD
Cement — Test methods —
Chemical analysis by X-ray fluorescence
This part of ISO 29581 describes a performance-based method for the chemical analysis of cement for SiO2,
Al2O3, Fe2O3, CaO, MgO, SO3, K2O, Na2O, TiO2, P2O5, Mn2O3, SrO, Cl and Br using X-ray fluorescence
(XRF). It can be applied to other relevant elements when adequate calibrations have been established.
This part of ISO 29581 describes an alternative method for analyses of cement for conformity and information purposes, based on beads of fused sample and analytical validation using certified reference materials, together with performance criteria.
A method based on pressed pellets of unfused sample can be considered as equivalent, providing that the analytical performance satisfies the same criteria.
The use of fused beads generally improves the accuracy of analysis for non-volatile elements, since it
eliminates variability arising from differences in mineralogical forms or oxidation states. Pressed pellets generally improve the accuracy of analysis for volatile elements and can give adequate accuracy for the routine analysis of non-volatile elements.
The presence of sulfide in a sample also leads to restrictions on the scope of the analysis that can be
undertaken using the XRF technique based upon fused beads. In particular, sulfate (SO3) cannot be determined directly
from such a fused bead because of the contribution to the analysis from the unknown amount of sulfide. In addition, sulfide cannot be determined directly (or accurately, indirectly) because of the contribution of the unknown amount of sulfate to the analysis and because of the possibility that some sulfide can be lost by volatilization during fusion. Consequently, the method of ISO 29581-1, included as Annex D to this part of ISO 29581, is the reference method for determining the sulfate content of samples containing sulfide species.
Other methods can be used, provided they are calibrated, either against the reference method or against internationally accepted reference materials, in order to demonstrate their equivalence.
In the case of dispute, unless otherwise agreed by al parties, only the reference method in ISO 29581-1 can be used.
This part of ISO 29581 describes methods that apply principally to cements, but which can also be applied to their constituent materials and to other materials, the standards for which call up these methods.
International Standard specifications state which methods can be used.
ISO 2010 – All rights reserved
ISO 29581-2:2010(E)
2 Normative
references
The following referenced documents are indispensable for the application of this document. For dated references, only the edition cited applies. For undated references, the latest edition of the referenced document (including any amendments) applies.
ISO Guide 30, Terms and definitions used in connection with reference materials
ISO Guide 31, Reference materials — Contents of certificates and labels
ISO 29581-1, Cement — Test methods — Part 1: Analysis by wet chemistry
EN 196-7, Methods of testing cement — Part 7: Methods of taking and preparing samples of cement
EN 197-1, Cement — Part 1: Composition, specifications and conformity criteria for common cements
3 Terms and definitions
For the purposes of this document, the following terms and definitions apply.
3.1
beads
glassy discs of fused sample for analysis by X-rays in the spectrometer
3.2
pellets
compressed discs of finely ground sample for analysis by X-rays in the spectrometer
3.3
calibration beads or pellets
beads or pellets used for establishing the calibration equation
3.4
analysis beads or pellets
beads or pellets containing the sample being analysed
3.5
accuracy
closeness of agreement between a test result and the certified value for a reference material
3.6
repeatability
closeness of agreement among independent test results obtained with the same method on identical test
items in the same laboratory by the same operator using the same equipment within short intervals of time
3.7
reproducibility
closeness of agreement between independent test results obtained with the same method on identical test
items in different laboratories with different operators using different equipment
3.8
expert laboratory
laboratory capable of consistently meeting the expert performance criteria set out in Clause 14
3.9
normal laboratory
laboratory capable of consistently meeting the normal performance criteria set out in Clause 14
ISO 2010 – All rights reserved
ISO 29581-2:2010(E)
4 General requirements for testing
4.1 Number
Analysis of a cement can require the determination of a number of its chemical elements. For each determination, one or more tests shall be carried out in which the number of measurements taken shall be as specified in the relevant clause of this part of ISO 29581.
Where the analysis is one of a series subject to statistical control, the determination of each chemical element by a single test shal be the minimum required.
Where the analysis method (including preparation and measurement) is checked at least once a week, as in accordance with 12.5.1, a determination of each chemical element by a single test shall be the minimum required. In the other cases, the number of tests for the determination of each chemical element shall be two; see also Clause 13.
4.2 Accuracy and precision limits
4.2.1 Accuracy
The accuracy performance criterion in this part of ISO 29581 is measured as a limit on the closeness of agreement between a test result and an accepted reference value for a certified reference material. The limits for accuracy, expressed in percent absolute, are set out in Table 2; one set is appropriate to the performance it is expected that an "expert" laboratory can achieve, whereas the other is appropriate for a "normal" laboratory.
4.2.2 Repeatability
The repeatability performance criterion in this part of ISO 29581 is measured as a limit on the repeatability where independent test results are obtained with the same method on identical test items (material) in the same laboratory by the same operator using the same equipment within a short interval of time. The limits for repeatability, expressed in percent absolute, are set out in Table 1; one set is appropriate to the performance it is expected that an "expert" laboratory can achieve, whereas the other is appropriate to a "normal" laboratory.
4.2.3 Reproducibility
The reproducibility performance criterion in this part of ISO 29581 is measured as a limit on the reproducibility where test results are obtained with the same method on identical test items (material) in different laboratories with different operators using different equipment. The limits for reproducibility, expressed in percent absolute, are set out in Table 3; one set is appropriate to the performance it is expected that an "expert" laboratory can achieve, whereas the other is appropriate to a "normal" laboratory.
4.2.4 Laboratory
competence
The laboratory shall demonstrate that it can achieve the required performance in accordance with 12.3.3 and 12.3.4.
4.3 Expression
Express mass in grams to the nearest 0,000 5.
4.4 Other
Other methods may be used, provided they are calibrated, either against the reference method or against internationally accepted reference materials, in order to demonstrate their equivalence.
ISO 2010 – All rights reserved
ISO 29581-2:2010(E)
5 Reagents and reference materials
reagents
Reagents shal be of analytical quality and, wherever possible, pure oxides or carbonates, except for the calibration of such elements as sulfur, chlorine, bromine or phosphorus, which do not form stable oxides or carbonates, where some guarantee of stoichiometry is required.
Reagents shall be free of (or corrected for) the presence of water (and, in the case of oxides, carbon dioxide) when weighed out for fusion. Also, the reagents shall be in a known oxidation state. The specified procedure ensures that the correct oxidation state is obtained.
The reagents used to prepare the standard beads for cations shall be pure oxides or carbonates of at least 99,95 % purity (excluding moisture or CO2).
Reagents shall be used in a known stoichiometry in terms of content. In order to achieve this, they can be treated before use as follows.
a) Determine the loss on ignition for silicon dioxide (SiO2), aluminium oxide (Al2O3) and magnesium oxide
(MgO) as fol ows.
1) Ignite the reagent at, for example, (1 175 ± 25) °C and maintain at this temperature for 30 min.
2) Cool in a desiccator to room temperature and reweigh.
3) After allowing for this loss, weigh the appropriate amount of the unignited material to prepare the
b) Dry manganese oxide (Mn2O3) and titanium(IV) oxide (TiO2) as follows.
1) Ignite the reagent at, for example, (1 000 ± 25) °C and maintain at this temperature for 30 min.
2) Cool in a desiccator to room temperature before use.
c) Dry iron (III) oxide (Fe2O3) as follows.
1) Ignite the reagent at, for example, (700 ± 25) °C and maintain at this temperature for 30 min.
2) Cool in a desiccator to room temperature before use.
d) Dry calcium carbonate (CaCO3), strontium carbonate (SrCO3), potassium carbonate (K2CO3) and sodium
carbonate (Na2CO3).
1) Heat the reagent at, for example, (250 ± 10) °C and maintain at this temperature for 2 h.
2) Cool in a desiccator to room temperature before use.
5.2 Reference
materials
5.2.1 Certified
reference
materials
Certified reference materials (CRMs) are materials, e.g. cement, supplied by an organization conforming to the requirements for the competence of reference material producers in accordance with ISO Guide 30.
CRMs shal be supplied with a certificate of analysis giving information on the average value and standard deviation in accordance with ISO Guide 31.
ISO 2010 – All rights reserved
ISO 29581-2:2010(E)
5.2.2 Industrial
reference
materials
Industrial reference materials (IRMs) are materials, e.g. cement, prepared and homogenized by a laboratory. The reference analysis of an IRM shal be the average result from inter-laboratory co-operative testing involving at least four laboratories able to meet the performance criteria given in 12.3.
5.3 Calibration
standards
Calibration standards are prepared in the laboratory from pure, analytical-grade reagents, IRMs, CRMs or a combination of these. They shall be formulated to provide a series of calibration standards covering the range of maximum to minimum values for each element being analysed and shall be evenly distributed between those limits. The variation in concentrations of the elements shall be independent of each other. There shall be a minimum of seven calibration standards in a series.
5.4 Binding
A binding agent, e.g. wax, whose influence on the elements being analysed has been determined, is used in the grinding of samples during the preparation of pressed pellets. Carry out a pellet-preparation monitoring check (see 12.5) whenever the batch of binding agent is changed.
6 Apparatus
6.1 Balance, capable of weighing to an accuracy of ± 0,000 5 g.
6.2 Fusion
and casting moulds, of a non-wetted platinum alloy, such as Pt/5 % Au or Pt/Rh.
Vessels that serve both as a fusion vessel and as a casting mould (i.e. a combined fusion mould) may be used. If moulds become distorted in use, then they shall be reshaped by pressing in a suitable former. If the bottom (flat) surface of the bead is used for analysis, it is necessary that the internal base of the mould also be kept flat and free from blemishes.
Cleanliness of fusion vessels is important in achieving accurate analyses. This can be achieved, for example,
by boiling in dilute hydrochloric acid, 1:10 by volume or citric acid, 100 g/l.
6.3 Lids, optional, of a platinum alloy (not necessarily non-wetted).
6.4 Furnace, e.g. an electric resistance, muffle or high-frequency induction furnace, capable of operating at
(250 ± 10) °C, (700 ± 25) °C, (950 ± 25) °C, (1 000 ± 25) °C and (1 175 ± 25) °C.
Automatic fusion apparatus, for use in automatic bead preparation (see 11.4).
An automatic fusion apparatus may be used, provided that the performance criteria in 12.3 can be met.
6.6 Cooling
apparatus, consisting of any device, such as a narrow jet of air that can be directed to the
centre of the base of the casting mould (for example, by the base of a bunsen burner without a barrel) or a water-cooled metal plate.
Normally, cooling in air is sufficient but some difficult samples can require a cooling apparatus in order to cool
the melt rapidly. This is necessary to obtain a homogeneous bead and to free the melt from the casting mould.
reservoir, for the casting mould, required in special circumstances when using moulds of small
sizes, so that the mould does not cool too rapidly when removed from the furnace.
6.8 Spectrometer, X-ray fluorescence, capable of meeting the performance criteria given in 12.3.
It is required to set appropriate measuring conditions to satisfy the performance criteria based on the type of
samples, the type of apparatus, elements being analysed and their content, etc.
ISO 2010 – All rights reserved
ISO 29581-2:2010(E)
gas, maintained at as constant a room temperature as possible.
The temperature of the flow gas cylinder and of the connecting pipework is critical in order to prevent drift in sensitivity of the flow proportional counters. Pipework shall be as short as practical and run, whenever possible, within the temperature-controlled room housing the spectrometer. Where this is not possible, the cylinder shal be kept in a temperature-controlled cabinet (room temperature ± 2 °C) or otherwise maintained
at a constant room temperature. For the same reason, new cylinders shall be allowed to equilibrate for at least 2 h to room temperature before use.
The flow gas is used in the gas flow proportional counter of the XRF spectrometer.
The composition of gas can change as the cylinder becomes exhausted. Cylinders should be replaced before
they become completely empty.
6.10 Grinding equipment, capable of grinding the sample, with binding agent if necessary, to a suitable
fineness.
6.11 Pellet press, capable of applying a pressure suitable for production of pellets with a consistent,
consolidated surface to meet the performance requirements given in 12.3.
6.12 Mould, usually of steel, of suitable strength to withstand the press without distortion and of suitable size
to produce a pellet to fit the spectrometer.
7 Preparation of a test sample of cement
Before chemical analysis, treat the laboratory sample, taken in accordance with EN 196-7, as follows to obtain a homogeneous test sample.
a) Take approximately 100 g of the laboratory sample by means of a sample divider or by quartering.
b) Sieve this portion on a 150 µm or 125 µm sieve until the residue remains constant.
c) Remove metallic iron from the material retained on the sieve by means of a magnet (see Note 1).
d) Grind the iron-free fraction of the retained material so that it completely passes the 150 µm or 125 µm
e) Transfer the sample to a clean, dry container with an airtight closure and shake vigorously to mix it
f) Carry out all operations as quickly as possible to ensure that the test sample is exposed to ambient air for
only the minimum time.
Where the analysis is one of a series subject to statistical control and the level of the metallic iron content has
been shown to be insignificant in relation to the chemical properties being determined, it is not necessary to remove metallic iron. Where the level of metallic iron is significant, it is required to record and report the amount in the results.
Where the sample contains quartz, it can be necessary to grind the sample to pass a 90 µm sieve in order to
obtain a satisfactory fusion (see Clause 11). The time and temperature required to obtain a satisfactory fusion is affected by the fineness of the sample.
Where pressed pellets are used, accuracy can be improved by grinding the sample more finely.
ISO 2010 – All rights reserved
ISO 29581-2:2010(E)
8.1 Choice of flux
8.1.1 General
One of the advantages of the XRF fused cast bead method is that a wide variety of fluxes may be chosen. For a given calibration, the same flux shall be used throughout. The conditions given in 8.1.2 to 8.1.4 shall be met for any flux used.
Fluxes used with success in the analysis of cement are given in Annex A. Pre-fused fluxes have the
advantage of a lower moisture content.
Reducing the particle size of the flux has been shown to improve fusion at a given temperature.
8.1.2 Dissolution
Under the conditions of preparation used, the sample shall be totally dissolved by the flux and shal not come out of solution in the casting procedure.
8.1.3 Heavy-element
absorber
A heavy-element absorber, such as lanthanum or vanadium oxide, may be incorporated into the flux, provided
⎯ it does not reduce sensitivities to the point that the performance criteria given in 12.3 cannot be met;
⎯ the heavy element does not have a line overlap with any of the elements being determined.
Lanthanum oxide assists the formation and stabilization of glass but reduces the intensity of the emitted
WARNING — There are restrictions on the use of heavy-metal chemicals in some countries. Care
should be taken in the handling of these and national safety rules observed.
8.1.4 Flux
The flux shall be pure with respect to the elements being determined.
Most reagents sold as "flux" grade quality by reputable manufacturers meet this requirement, but an analysis shall be obtained for each batch of flux supplied. Carry out a bead-preparation monitoring check (see 12.5) when a batch of flux is changed.
8.2 Moisture in flux
Pre-molten fluxes having a loss on ignition not exceeding 0,50 % mass fraction are preferred. However, if the flux contains moisture, it shall be dried at a suitable temperature.
8.3 Flux-to-sample
The flux-to-sample ratio selected shall be such that the performance criteria given in 12.3 are met. The mass fraction ratio, R, of flux to sample used for the calibration shall be used for subsequent analyses.
As the flux-to-sample mass fraction ratio is greater than one, impurities in the flux can have a negative
influence on the measured result. The greater the ratio of the flux to sample, the greater the influence.
The total mass of sample and flux shall be chosen for the particular casting mould type used, and this mass shall always remain the same.
ISO 2010 – All rights reserved
ISO 29581-2:2010(E)
8.4 Anti-wetting
A small amount of anti-wetting agent may be used, if necessary. An anti-wetting agent, such as lithium bromide, ammonium bromide, lithium iodide, lithium iodate or ammonium iodide, may be added to the melt to assist in preventing the cracking of the fused beads on cooling and to aid in the release from the mould. Where an anti-wetting agent is used, all beads shal be prepared using the same anti-wetting agent added in the same quantity and at the same stage of bead preparation.
Bromine or iodine in the anti-wetting agent can remain in the bead under some fusing conditions. It is required
to check for residual bromine or iodine, since these elements can cause line overlapping, such as Br Lα on Al Kα or I Lβ2
9 Determination of loss on ignition and the change in mass on fusion of the cement
9.1 Principle
In order to be able to total (to 100 % mass fraction) any oxide analysis of cement, a loss on ignition, i.e. the amount of any combined water and carbon dioxide, is required. In addition, in order to be able to convert an oxide analysis obtained on the fused-basis using fused-bead XRF, to an oxide analysis on the as-received basis, an "observed" loss on ignition is also required.
Where the sample contains no oxidizable species, the loss on ignition and the "observed" loss on ignition are
The "observed" loss on ignition (see 9.3.1) is a very close approximation to the "change in mass on fusion" that occurs when a sample is prepared as a fused bead for analysis by XRF. This "observed" loss on ignition is used in this method to calculate a factor, f, (see Clause 10) to convert test results obtained on the fused basis to the as-received basis.
The traditional loss-on-ignition determination carried out in an oxidizing atmosphere by igniting in air can be used to determine both the loss on ignition and the "observed" loss on ignition. Where any oxidizable species are present, in particular sulfide or sulfur-containing species, a correction can be applied to the "observed" loss in order to derive a "corrected" loss on ignition for use in totalling the oxide analysis. However, any error resulting from the oxidation of any metallic iron, bivalent iron or bivalent manganese is usually considered to be negligible and only the correction for the extent of oxidation of sulfides is applied in the correction.
An alternative method, e.g. automatic equipment, may be used, provided that it can be demonstrated that the performance criteria given in 12.3 are satisfied.
9.2 Procedure
Weigh, to ± 0,000 5 g, (1,00 ± 0,05) g of cement into a crucible which has been previously ignited and tared.
Record this mass as m1. Place the covered crucible in the furnace (6.4) controlled at (950 ± 25) °C. After
heating for 5 min, remove the lid and leave the crucible in the furnace for a further 10 min. Allow the crucible to cool to room temperature in a desiccator. Determine constant mass by making successive 15 min ignitions followed each time by cooling and then weighing, and record as m2. Constant mass is reached when the
difference between two successive weighings is less than 0,000 5 g.
For cements containing sulfides, a more accurate determination of the loss on ignition can be obtained by
determining the sulfate content before and after ignition. The correction applicable to these cements is given in 9.3.2.
When vacuum desiccators are used, the appropriate desiccator inlet trap should be used when any vacuum is released. Phosphorus pentoxide should be avoided where surface-active materials are being stored, since P2O5 can be absorbed by the sample, particularly under vacuum conditions.
ISO 2010 – All rights reserved
ISO 29581-2:2010(E)
9.3 Calculation and expression of results
9.3.1 Observed loss on ignition
Calculate the observed loss on ignition (i.e. the change in mass on fusion), L, expressed as a percentage mass fraction, as given in Equation (1):
m − m
m1 is the mass of the test portion, expressed in grams;
m2 is the mass of the ignited test portion, expressed in grams.
9.3.2 Correction to the observed loss on ignition for the oxidation of sulfides
Calculate the correction to the "observed" loss on ignition for the extent of oxidation of sulfides, by determining the sulfate present before and after ignition. The gravimetric method of ISO 29581-1, reproduced in Annex D of this part of ISO 29581, is the reference method for these sulfate determinations.
The amount of SO3, wS,up, resulting from the oxidation of sulfides, expressed as a percentage mass fraction,
is calculated as given in Equation (2):
wS,up = wS,f − wS,i
wS,f is the final SO3 value, expressed as a percentage mass fraction;
wS,i is the initial SO3 value, expressed as a percentage mass fraction.
A correction, wO,up, for the oxygen taken up by the test portion, expressed in percent, is given by Equation (3):
wO,up = 0,8 wS,up
The corrected loss on ignition, Lcor, is calculated as given in Equation (4):
Lcor = L + wO,up
where L is the observed loss on ignition, expressed as a percentage mass fraction.
Indicate any corrections applied in the test report.
9.4 Repeatability and reproducibility for loss on ignition
The standard deviation for repeatability is 0,04 % mass fraction.
The standard deviation for reproducibility is 0,08 % mass fraction.
ISO 2010 – All rights reserved
ISO 29581-2:2010(E)
10 Factoring test results and correcting total analyses for presence of sulfides and
halides
10.1 General
Analyses may be carried out on a fused-bead or pressed-pellet test portion. In the case of analysis using fused beads, it is necessary to determine the change in mass that occurs during fusion (see 9.3.1) in order to derive a multiplying factor for converting test results obtained on the fused basis to analytical results reported on the as-received basis.
In addition, where sulfide, chloride or bromide are present, it is also necessary to correct the total oxide analysis of a cement for the fact that, traditionally, these species are also expressed as if they were oxygen (combined with calcium) in the analytical result reported for calcium oxide. This latter correction also applies to analyses carried out using pressed pellets.
10.2 Factoring test results obtained from fused-bead analysis
10.2.1 Principle
Where fusion is employed, it is necessary to determine the change in mass that occurs during fusion in order to derive a multiplying factor for converting test results obtained on the fused basis to analytical results on the as-received basis.
The change in mass that occurs during fusion is determined by igniting, in air, a weighed test portion to constant mass at (950 ± 25) °C and calculating the "observed" loss on ignition; see 9.3.
The change in mass occurring during fusion in air is normally a loss as, generally, water and carbon dioxide
are released. Where, however, the sample contains oxidizable species, there is an increase in mass of these species during fusion resulting from oxygen uptake. This might or might not lead to an overall increase in mass of the test portion depending on the balance of mass lost versus mass gained. The oxidizable species that can lead to an overall gain in mass of a test portion is sulfur, generally present as sulfide (typically calcium sulfide) in test portions that contain a blast-furnace slag constituent. Other oxidizable species, where present, such as metallic iron, bivalent iron or bivalent manganese, are generally present in small amounts and make only a minor contribution to mass change.
The presence of sulfide in a sample also leads to restrictions on the scope of the analysis that can be
undertaken using the XRF technique based upon fused beads. In particular, sulfate (SO3) cannot be determined directly
from such a fused bead because of the contribution to the concentration from the unknown amount of sulfide. In addition, sulfide cannot be determined directly (or accurately, indirectly) because of the contribution of the unknown amount of sulfate to the analysis and from the possibility that some sulfide could have been lost by volatilization during fusion. Consequently, the method of ISO 29581-1, included as Annex D to this part of ISO 29581, is the reference method for determining the sulfate content of samples containing sulfide species.
10.2.2 Calculating the factor for converting the results obtained using fused beads
Calculate the factor, fLOI, for converting test results obtained on the fused basis to analytical results on the
as-received basis, from the observed loss on ignition, L, (see 9.3.1) as given in Equation (5):
⎛ 100 − L ⎞
fLOI = ⎜
where L is expressed as a percentage mass fraction.
When L is a negative number, which occurs when the test portion has undergone an overall gain in mass, preserve the sign together with L in Equation (5).
ISO 2010 – All rights reserved
ISO 29581-2:2010(E)
10.2.3 Use of the conversion factor, fLOI
Convert all test results obtained on the fused basis to analytical results on the as-received basis by multiplying
each result by the factor, fLOI.
10.3 Correcting total oxide analysis for sulfides and halides
10.3.1 Correcting total oxide analysis for sulfides
Irrespective of whether the analysis was carried out on a fused (bead) or pressed (pellet) test portion, determine the sulfide content of the cement, on the as-received basis, in accordance with the method for sulfide determination in ISO 29581-1.
The factor, fS, to correct the total analysis of cement containing sulfide species, is calculated as given in
fS = ws2− + Lcor + wO,tot − wO,s2− (6)
is the sulfide content, expressed as a percentage mass fraction;
Lcor
is the "corrected" loss on ignition, expressed as a percentage mass fraction; see 9.3.2;
wO,tot is the sum of all oxides, expressed as a percentage mass fraction; see Clause 1;
wO,s2− is the oxygen equivalent of sulfide, expressed as a percentage mass fraction, which is calculated
as given in Equation (7):
wO,s2− = 0,5ws2− (7)
10.3.2 Correcting total oxide analysis for halides
10.3.2.1 Correcting total oxide analysis for chloride
Irrespective of whether the analysis has been carried out on a fused (bead) or pressed (pellet) test portion, calculate the factor, fCl, to correct the total analysis of cement containing chloride as given in Equation (8):
fCl = wCl + Lcor + wO,tot − wO,Cl
the chloride content, expressed as a percentage mass fraction;
wO,Cl is the oxygen equivalent of chloride, expressed as a percentage mass fraction, which is
calculated as given in Equation (9):
wO,Cl = 0,2wCl (9)
Any correction for the presence of chloride is generally very small and is usually ignored.
ISO 2010 – All rights reserved
ISO 29581-2:2010(E)
10.3.2.2 Correcting total oxide analysis for bromide
Irrespective of whether the analysis has been carried out on a fused (bead) or pressed (pellet) test portion, calculate the factor, fBr, to correct the total analysis of cement containing bromide as given in Equation (10):
fBr = wBr + Lcor + wO,tot − wO,Br
where wBr is the bromide content, expressed as a percentage mass fraction, which is calculated as given in
wBr = 10 wO,Br
Any correction for the presence of bromide is generally very small and is usually ignored.
11 Preparation of fused beads and pressed pellets
11.1 General
At several of the stages, a choice of procedures is given. Once a choice has been made, the procedure shall be adhered to throughout calibration and analysis, unless a new calibration is carried out in accordance with Clause 12.
The bead or pellet preparation conditions shall be set such that the criteria given in 12.3 are met.
11.2 Conversion of the sample to bead form
11.2.1 Weighing of the sample
11.2.1.1 General
Weigh the sample, the flux and any anti-wetting agent to the nearest 0,000 1 g and to the ratio, R, selected. Add the anti-wetting agent, when used as a solution, using a micro-pipette. The sample being used shall be weighed as given in either 11.2.1.2 or 11.2.1.3.
11.2.1.2 Unignited
The required mass, m3, expressed in grams, of the unignited sample is calculated as given in Equation (12):
m4 is the mass of fused sample (see 8.3) required to prepare a bead, expressed in grams;
is the observed loss on ignition, expressed in percent (see 9.3.1).
11.2.1.3 Ignited
Prepare the sample in accordance with 9.2 but, in this case, the appropriate amount of the sample may be used. A constant mass is reached when the difference between two successive weighings is less than 0,05 % mass fraction. Store ignited samples in a desiccator.
When preparing a bead using the ignited sample, carry out weighings as quickly as possible to avoid contamination.
ISO 2010 – All rights reserved
ISO 29581-2:2010(E)
Where the sample contains significant amounts of carbonate that can result in loss of material through spurting, or where it contains carbides, iron or other metals that can interact with platinum and damage the crucible, the ignited sample should be used in the preparation of beads.
The amount of the sample should not be more than 5 g, because it is difficult with a larger sample to reach a constant mass without repeated ignitions. However, if a large amount of sample is being used, lumps in the sample should be broken up after the first ignition.
11.2.2 Fusion procedure
Thoroughly mix the sample, the flux and any anti-wetting agent before fusion. Where the anti-wetting agent is added as a solution, it shall be added after placing the mixture of sample and flux into the fusion vessel and evaporating all moisture at a low temperature before the fusion. Fuse the mixture for the prescribed time, e.g. 10 min, at the selected, controlled temperature with occasional swirling until the sample dissolves and the melt is homogeneous.
The volatilization of sulfur trioxide becomes significant for samples fused at temperatures in excess of
1 100 °C. Where sulfur trioxide is being determined, it is essential to keep the temperature below this level.
The fusion temperature may be specified according to cement or element type. For more volatile elements, e.g. sulfate, sulfide, chloride or alkalis, fusion at reduced temperature or the use of pressed pellets can be necessary to achieve the required precision.
Increasing the temperature in two stages has been shown to improve precision.
11.3 Casting of the beads
11.3.1 General
Cast the beads using one of the following methods. Beads produced shall be free from blemishes on the analytical measuring surface.
a) Outside the furnace: after 5 min, remove the casting mould (and the heat reservoir) from the furnace and
place on a horizontal surface. Remove the lid from the fusion dish, remove the dish from the furnace and immediately pour the melt into the casting mould.
a) In the furnace: after 5 min, remove the lid from the fusion dish and pour the melt into the casting mould
inside the furnace, ensuring that as much of the melt is transferred to the casting mould as possible. Remove the casting mould from the furnace and place on a horizontal surface.
b) Combined fusion mould: after 5 min, remove the fusion mould from the furnace and by swirling ensure the
transfer of the whole of the melt into the mould part of the dish.
c) Mould heated over burner: after preparation of the melt, pour the melt into the preheated casting mould
and turn the burner off.
d) Inside the fusion mould: after completion of the fusion, leave the melt inside the fusion dish and remove it
from the furnace.
11.3.2 Cooling of the beads
Allow the casting mould to cool on a horizontal surface.
If rapid cooling is required, when the melt has cooled from red heat, transfer the casting mould to an air jet (6.6) (or alternatively, a water-cooled plate). The melt can be molten or solid at this stage. Hold the dish in a horizontal position above the air jet so that the air is directed onto the centre of the base of the mould. When the bead has solidified and released itself, turn off the air jet.
It can be necessary to encourage the release of the beads at this stage by gently tapping the casting mould on
a solid surface.
ISO 2010 – All rights reserved
ISO 29581-2:2010(E)
11.4 Automatic bead preparation
An automatic fusion apparatus (6.5) may be used to prepare beads.
11.5 Storage
Protect beads from deterioration caused by adverse temperature and humidity conditions, e.g. by storage in a polyethylene self-seal bag. If the laboratory environment is suitably controlled (e.g. air-conditioned), then the bag shall be stored in a desiccator. Alternatively, if the environment is not controlled, the bags shall be stored in a temperature-controlled oven at 25 °C to 30 °C.
Where pressed pellets are being stored for a limited period, they may be placed unwrapped in a desiccator.
The bags themselves can cause surface contamination due to the use of "anti-blocking agents" (the effect being more apparent for the lighter elements). After long-term storage, thoroughly clean the measuring surfaces of beads before use, e.g. by washing with ethanol or acetone or by polishing.
Reported sources of contamination are as follows:
⎯ sulfur from vacuum oil in the spectrometer or from the laboratory atmosphere;
⎯ sodium and chlorine from the atmosphere if the laboratory is near the sea;
⎯ sodium from manual contact;
⎯ potassium from cigarette smoke.
11.6 Pressed pellets
Weigh, to the nearest 0,1 g, a quantity of sample suitable to fill the mould to excess. Grind to a suitable fineness, with a binding agent (5.4) if necessary. Place the ground sample into the pellet mould (6.12) and spread evenly. Apply pressure at a rate and for a time shown to be suitable to ensure that the criteria given in 12.3 are met. Store in accordance with 11.5 until required.
12 Calibration and validation
12.1 Principles
The calibration equations and inter-element corrections are established using calibration standards produced using beads or pellets made from pure reagents, CRMs, IRMs or any combination of these (see Clause 5). The validity of the calibration is confirmed by analysing one or more CRMs, representative of the range of analyses being undertaken. The ongoing calibration monitoring for intensity, bead preparation and calibration drift is determined immediately after calibration and at intervals during the analytical process. Typical ranges for calibration standards for analysis of CEM I cements are given in Annex C. Examples of sources of CRMs are shown in Annex B. Performance criteria are set out in Clause 14.
12.2 Calibration and validation samples
12.2.1 Calibration standards
Prepare a series of beads or pellets from pure reagents, IRMs, CRMs or combinations of these (see Clause 5) as calibration standards. The series shal cover the range from the minimum to the maximum values for each element being analysed and shall be evenly distributed between those limits. The variations in the concentration of each element in the calibration standard shall be independent of each other. The minimum number of standards is seven.
ISO 2010 – All rights reserved
ISO 29581-2:2010(E)
An example of a series of calibration standards suitable for the analysis of cements of type CEM I, in accordance with EN 197-1, is given in Annex C. Other reagents may be added to cover the scope of the elements being determined.
Where ten standards or fewer are used, duplicate beads or pellets should be prepared. Where a larger number of standards is used, single preparation can be sufficient.
For pellet analysis, a calibration made from IRMs or CRMs can provide unsatisfactory results due to mineralogical effects. In this case, the calibration may be done with secondary standards, made from samples routinely analysed by the laboratory, that have been characterized with at least one analysis by reference methods or by X-ray fluorescence using fused beads.
12.2.2 Calibration validation of a CRM or IRM
Prepare one or more CRMs, not used in the calibration standard (12.2.1) and having a composition within the calibration range for each element being analysed.
When only one validation CRM is being used, select a sample in the middle of the concentration ranges. Where several validation CRMs are used, select samples covering high and low values.
Examples of sources of CRMs are given in Annex B.
If no suitable CRM is available, choose an IRM that satisfies the above criteria. It is recommended that each IRM be validated by at least four laboratories.
In the case of pressed pellets, and especially for composite cements, variations in mineralogy can affect the
accuracy. In such cases, it is necessary to use an IRM matching closely each type of sample being analysed, and preferably made from the samples routinely analysed by the laboratory.
12.2.3 Intensity correction samples
These are sometimes referred to as "monitor" samples.
Use one or more samples, (glass beads or other stable material) each having a composition giving an intensity level similar to the calibration range for each element being analysed. If several samples are used, select high and low values for each element. These samples shall be different from the calibration standards (see 12.2.1). Store these samples for future reference. Excessive exposure to the X-ray beam shall be avoided to prevent ageing.
Samples stored as pellets are subject to rapid ageing and, therefore, it is recommended that fused beads or
glass be used for intensity control, even where the analysis predominantly uses pellet calibrations.
The samples shall be used to calculate a correction factor to apply to the raw intensity measurements, to take account of the ageing of the apparatus (X-ray tube, detectors, etc.) (see 12.4.3).
12.2.4 Re-calibration standards
Select two of the calibration standards (12.2.1), having high and low values for each element of interest, and store for future reference.
Depending on the equipment, it can be required to define re-calibration standards at the time of the initial
They shall be used to adjust the equation of the calibration curve in the event that the drift of the apparatus is not sufficiently corrected by the intensity correction procedure (see 12.4.4).
ISO 2010 – All rights reserved
ISO 29581-2:2010(E)
12.2.5 Spectrometer control samples
12.2.5.1 Control for bead analysis
Prepare and store one or more beads within, or close to, the calibration range. Calibration validation samples (see 12.2.2) are suitable.
A replacement bead may be prepared if ageing is suspected.
12.2.5.2 Control for pellet analysis
Due to the more rapid ageing of pellets, it is not possible to ensure control of the spectrometer using pellets. Therefore, the spectrometer control for pellet analysis shall be made using a fused bead or glass sample.
12.2.6 Preparation procedure control sample
Prepare a new bead or pellet of the calibration validation samples (see 12.2.2) as a control for the preparation procedure.
12.3 Initial calibration
12.3.1 Calibration procedure
Establish the calibration relationship between the intensity of measured X-rays and the element concentration, including corrections for any mass absorption and line overlap effects.
At a reasonable counting time (e.g. 200 s), measure and record the intensities for each element being determined in al of the calibration beads or pellets. Using regression analysis, establish the calibration curve for each element being determined.
Increasing the counting time on the measurement of the standards can improve the accuracy of the calibration.
12.3.2 Calibration for inter-element effects
Where inter-element effects significantly influence the accuracy of the calibration, e.g. the influence of potassium on calcium, it can be necessary to establish a correction. For each inter-element correction applied, prepare at least one additional calibration standard bead or pellet.
12.3.3 Validation of calibration
Validate the accuracy of the calibration for the elements being determined by analysing, in duplicate, at least one accuracy validation sample [see 12.2.2 (CRM or IRM)].
When selecting a CRM for validation, it is recommended that the series of analyses used to produce the
certified analysis be examined in relation to the criteria for repeatability, reproducibility and accuracy (see Clause 14).
The calibration is valid if all the elements being determined satisfy the accuracy limits set down in Table 2.
If the calibration is not valid:
⎯ consider the need for a calibration adjustment for inter-element effects (see 12.3.2);
⎯ consider whether the set of standards used is adequate;
⎯ determine other cause(s), and take appropriate corrective action; or,
⎯ repeat initial calibration in accordance with 12.3, as appropriate.
ISO 2010 – All rights reserved
ISO 29581-2:2010(E)
Figure 1 — Calibration validation
12.3.4 Validation of repeatability
12.3.4.1 General
Validate the repeatability of analysis for a new spectrometer or when there has been any major modification of the preparation procedure or the spectrometer.
ISO 2010 – All rights reserved
ISO 29581-2:2010(E)
12.3.4.2 Repeatability of the spectrometer
Measure, over a period of not more than one week, the same bead of the spectrometer control sample (see 12.2.5) at least 10 times. Record the average and calculate the standard deviation of these measurements. To validate the spectrometer repeatability, the standard deviation shall be less than one-third of the repeatability limits defined in Table 1.
The limits in Table 1 allow for the overal procedure repeatability. The repeatability of the spectrometer itself should be lower, to ensure the required repeatability of the method.
If the repeatability of the spectrometer is not validated, implement one of the following and repeat the repeatability validation:
⎯ check the stability of the apparatus (gas flow, temperature regulation, etc.);
⎯ increase the counting time;
⎯ increase the sample-to-flux ratio for the bead to improve sensitivity.
12.3.4.3 Repeatability of the method
Prepare, over an appropriate period of time (e.g. at least two weeks), at least 10 different preparations of the preparation procedure control sample (see 12.2.6). Record the average and the calculated standard deviation.
The repeatability of the method is valid if the difference in results for each new preparation, compared with the previous example, is within the repeatability limits defined in Table 1.
If the repeatability of the method is not validated:
⎯ check the stability of the apparatus (gas flow, temperature regulation, etc.);
⎯ increase the counting time;
⎯ increase the sample-to-flux ratio for the bead to improve sensitivity;
⎯ increase the fineness of the sample;
⎯ increase the temperature and/or duration of the fusion for beads;
⎯ consider the use of a grinding agent or binding wax for pellets;
⎯ increase the duration and/or pressure on the press for pellets.
12.3.5 Initial values of the intensity correction samples
At the time of the initial calibration, record the initial values of the intensity correction samples ("monitors"; see 12.2.3).
It is generally possible to store these values in the software.
Store the corresponding samples for future reference.
12.3.6 Initial values of the re-calibration standards
At the time of the initial calibration, record the initial values of the re-calibration standards (see 12.2.4).
It is generally sufficient in the software to define two of the calibration standards (see 12.2.1) as the re-
calibration standards.
ISO 2010 – All rights reserved
ISO 29581-2:2010(E)
12.3.7 Initial values of the spectrometer control sample
At the time of the initial calibration, record the average value, calculated in accordance with 12.3.4.2, of the spectrometer control sample (see tolerance limits in 12.4.2).
If ageing of the spectrometer control sample is suspected, prepare a new bead, and establish new initial
12.3.8 Initial values of the preparation procedure control sample
At the time of the initial calibration, record the average calculated in 12.3.4.3 as the initial value of the preparation procedure control sample (see 12.2.6 and preparation repeatability validation limits in 12.5.1).
12.4 Spectrometer follow-up
12.4.1 Principle
The main bias in X-ray fluorescence is the intensity drift due to ageing. The consistency of the results is monitored by measuring the spectrometer control sample (see 12.2.5), before carrying out each series of sample analyses.
In the first instance, this intensity drift is corrected using the intensity correction samples (12.2.3). Where this is not sufficient, correction factors may be applied to the calibration equation using the re-calibration standards. Alternatively, a full re-calibration can be necessary.
After each action that modifies the result provided by the spectrometer (e.g. drift correction or re-calibration), the accuracy shall be assessed again in accordance with 12.3.3.
12.4.2 Spectrometer follow-up validation
12.4.2.1 General
If the spectrometer control sample is within the limits set out below, or if the calibration has been re-validated in accordance with 12.3.3, then the spectrometer is ready for analysis. If the analysis is not valid, apply the decision diagram in Figure 2.
12.4.2.2 Re-validation of bead calibration
The bead calibration remains valid if the results, compared with the initial values (see 12.3.7), are equal to or less than three times the standard deviation for the spectrometer determined in 12.3.4.2.
12.4.2.3 Re-validation of pellet calibration
Depending on the capabilities of the software used, record the measurements
⎯ as a corrected intensity, taking into account the intensity drift correction (see 12.4.4);
⎯ as a concentration.
The pellet calibration remains valid if the results, compared with the initial values (see 12.3.7), are equal to or less than three times the standard deviation for the spectrometer determined in 12.3.4.2.
ISO 2010 – All rights reserved
ISO 29581-2:2010(E)
Figure 2 — Analysis validation decision schemeInstrument check
Carry out the following checks, as necessary:
⎯ whether any automatic fine adjustment, present in software on some spectrometers, has been made;
⎯ resolution counter problems;
⎯ 2-theta angle settings;
⎯ high-voltage settings of the detector.
ISO 2010 – All rights reserved
ISO 29581-2:2010(E)
12.4.3 Correction for intensity drift
Where necessary (see Figure 2), a correction factor is calculated for each element to compensate for the drift in intensity due to ageing of the tube, detector, etc. Subsequently, the corrected intensities are then used in the calibration equation to derive the concentrations.
In most software applications, this correction is applied to all calibrations for each element.
The intensity drift should be small and regular with time. A sudden drop in intensity indicates an instrumental problem, and correction by this intensity drift method is not appropriate.
12.4.4 Re-calibration
Where necessary (see Figure 2), if the intensity correction (see 12.4.4) is insufficient to achieve accurate results for the analysis validation (see 12.4.2), it is possible to apply correction factors to the calibration curves using the re-calibration standards.
The modifications in the calibration equation due to instrumental drift should be small and regular with time. Any rapid or major bias in the analytical results can indicate an instrumental or analytical problem, and correction by this re-calibration method is not appropriate.
12.5 Preparation procedure follow-up
12.5.1 Bead and pellet preparation validation
On a regular basis, the whole analysis method shall be checked, including preparation of the bead or pellets and the measurement on the spectrometer.
Prepare a new preparation procedure control sample (see 12.2.6). The preparation is valid if
⎯ the results of the new analysis, compared with the initial values (see 12.3.8), are within the limits for
repeatability set down in Table 1;
⎯ the ongoing average values for new analyses, compared with the certified values of the CRM or IRM, are
within the limits for accuracy set down in Table 2.
12.5.2 Remedial action for preparation bias
If the analysis fails to satisfy the repeatability or accuracy limits set down in 12.5.1, check whether
⎯ the flux is loss-on-ignition-free;
⎯ drift can have occurred due to the preparation apparatus (check temperature, fineness, quality of sample
⎯ a new batch of flux has been introduced;
⎯ a new bead or pellet preparation apparatus has been installed;
⎯ the sample preparation procedure has been changed or modified, e.g. from manual to automatic;
⎯ a new type of flux or new sample-to-flux ratio has been used;
⎯ other procedural or apparatus changes have been introduced.
In the first two cases, take remedial action and re-check the analysis.
In al other cases, carry out a full re-calibration, including new preparation of al of the samples in accordance with 12.2.
ISO 2010 – All rights reserved
ISO 29581-2:2010(E)
Table 1 — Repeatability limits for analysis validation
Repeatability limit
Repeatability limit for
Element mean value
for "normal" performance
"expert" performance
% mass fraction absolute
% mass fraction absolute
All values of repeatability are expressed on the basis of fused, i.e. loss-on-ignition-free, samples.
Table 2 — Accuracy limits for validation
Accuracy limit
Accuracy limit
Content of element species
for "normal" performance
for "expert" performance
% mass fraction absolute
% mass fraction absolute
% mass fraction absolute
All values of accuracy are expressed on the basis of fused, i.e. loss-on-ignition-free, samples.
ISO 2010 – All rights reserved
ISO 29581-2:2010(E)
Table 3 — Reproducibility limits achieved using certified reference materials
Element mean value
Reproducibility limit
Reproducibility limit
for "normal" performance
for "expert" performance
All values of reproducibility are expressed on the basis of fused, i.e. loss-on-ignition-free, samples.
13 Calculation and expression of results
Calculate the concentrations on a fused basis from the calibration curve (see 12.3.1), corrected, where necessary, for any inter-element effect (see 12.3.2).
Calculate the results, where a single test result has been obtained, as a percentage mass fraction to four significant figures when the value exceeds 1,00 % mass fraction, or to three decimal places for values below 1,00 % mass fraction.
Calculate the results, where two test results have been obtained, as the mean of the results, as a percentage mass fraction to four significant figures when the value exceeds 1,00 % mass fraction, or to three decimal places for values below 1,00 % mass fraction.
If the two test results differ by more than the appropriate repeatability limits set out in Table 1, repeat the test and take the mean of the two closest test results.
ISO 2010 – All rights reserved
ISO 29581-2:2010(E)
Convert test results on a fused basis to results on the as-received basis using the factor, fLOI, in accordance
Where the sample contains oxidizable sulfur species, or any chloride or bromide, see 10.3 with regard to totalling the oxide analysis.
The results of all individual tests shall be recorded.
Express the results, general y as the oxide, to two decimal places.
14 Performance criteria (repeatability, accuracy and reproducibility limits)
Performance criteria are given in Tables 1, 2 and 3.
ISO 2010 – All rights reserved
ISO 29581-2:2010(E)
Examples of fluxes
There are three examples of fluxes that have proved suitable:
a) 66 % lithium tetraborate +34 % lithium metaborate; purity 99,95 % (minimum);
b) 100 % lithium tetraborate; nominal 100 %;
tetraborate/lithium metaborate, in ratios of 100/0 to 0/100 %; purity 99,98 %.
ISO 2010 – All rights reserved
ISO 29581-2:2010(E)
Sources of certified reference materials
Examples of sources of certified reference materials include the following:
Community Bureau of Reference (Belgium);
British Chemical Standards (UK);
Canada Centre for Mineral and Energy Technology (Canada);
Dillinger Laboratory (Germany);
Euronorm Certified Reference Materials (EU);
State Bureau of Technical Supervision (China);
Iron and Steel Institute of Japan (Japan);
National Council for Cement and Building Materials (INDIA);
National Institute of Standards and Technology (USA);
South African Bureau of Standards (South Africa); and
BREITLÄNDER Eichproben + Labormaterial GmbH (Germany).
1) This is an example of a suitable commercial supplier. This information is given for the convenience of users of this part of ISO 29581 and does not constitute an endorsement by ISO.
ISO 2010 – All rights reserved
ISO 29581-2:2010(E)
Examples of calibration standards and monitor beads and pellets
Table C.1 — Calibration standards for the calibration of analysis of CEM I cements
Mass of reagents required for each fusion
Bead number
Table C.2 — Composition of the calibration standards listed in Table C.1
Composition
Bead number
ISO 2010 – All rights reserved
ISO 29581-2:2010(E)
Determination of the sulfate content
of samples containing sulfide species
D.1 Principle
Sulfate ions, produced by the decomposition of cement with hydrochloric acid, are precipitated at a pH between 1,0 and 1,5 by a solution of barium chloride. The precipitation of barium sulfate is carried out at boiling point.
The determination is then completed gravimetrically and sulfate expressed as SO3.
D.2 Reagents and equipment
D.2.1 Hydrochloric
acid (HCl), concentrated, density 1,18 to 1,19.
D.2.2 Hydrochloric
acid, dilute, 1 + 11.
D.2.3 Ammonium
hydroxide, dilute, 1 + 16.
D.2.4 Barium
chloride, solution, prepared by dissolving 120 g of barium chloride (BaCl2.2H2O) in water
and making up to 1 000 ml.
D.2.5 Silver
nitrate, solution, prepared by dissolving 5 g of silver nitrate (AgNO3) in water, adding 10 ml of
concentrated nitric acid (HNO3) and making up to 1 000 ml with water.
D.2.6 Filter
paper, ashless.
Filter papers with a mean pore diameter of around 2 µm are termed fine, those with a mean pore diameter of
around 7 µm are termed medium and those with a mean pore diameter of around 20 µm are termed coarse.
D.3 Procedure
Weigh, to ± 0,000 5 g, (1,00 ± 0,05) g of cement and record this mass as m5. Place the cement sample in a
250 ml beaker, and add 90 ml of water. While stirring the mixture vigorously, add 10 ml of concentrated hydrochloric acid (D.2.1). Heat the solution gently and crush the sample with the flattened end of a glass stirring rod until decomposition is complete. Allow the solution to digest for 15 min at a temperature just below boiling.
Filter the residue on a medium filter paper (D.2.6) into a 400 ml beaker. Wash thoroughly with hot water until free from chloride ions, as determined by the silver nitrate test (D.7).
Adjust the volume to about 250 ml; if necessary, adjust the pH of the solution to between 1,0 and 1,5 with dilute hydrochloric acid 1 + 11 (D.2.2) or ammonium hydroxide 1 + 16 (D.2.3).
Bring to a boil and boil for 5 min. Check that the solution is clear; if not, start the determination again using a new test portion. While stirring vigorously, maintain the solution at the boiling point and add, drop by drop, 10 ml of the barium chloride solution (D.2.4) heated to just below boiling. Maintain the solution at just below boiling point for at least 30 min, ensuring that the volume is kept between 225 ml and 250 ml, and then allow the covered beaker to stand at room temperature for 12 h to 24 h before filtration.
ISO 2010 – All rights reserved
ISO 29581-2:2010(E)
Filter the precipitate on a fine filter paper (D.2.6) and wash with boiling water until free from chloride ions, as determined by the silver nitrate test (D.7).
Ignite at (950 ± 25) °C to constant mass (D.6) and record this mass as m6.
In general, an ignition period of 15 min is sufficient to achieve constant mass.
D.4 Calculation and expression of results
Calculate the sulfate content, expressed as SO3, in percent, using the equation:
m6 × 0,343 ×100
= 34,3 × m5
m5 is the mass of the test portion, expressed in grams;
m6 is the mass of barium sulfate, expressed in grams.
D.5 Repeatability and reproducibility
The standard deviation for repeatability is 0,07 % mass fraction.
The standard deviation for reproducibility is 0,08 % mass fraction.
D.6 Determination of constant mass
Determine constant mass by making successive 15 min ignitions followed each time by cooling and then weighing. Constant mass is reached when the difference between two successive weighings is less than 0,000 5 g.
D.7 Check for absence of chloride ions (silver nitrate test)
After five to six washes of a precipitate, rinse the base of the filter stem with a few drops of water. Wash the filter paper and its contents with several millilitres of water and collect this in a test tube. Add several drops of silver nitrate solution (D.2.5). Check the absence of turbidity or precipitate in the solution. If present, continue washing while carrying out periodic checks until the silver nitrate test is negative.
ISO 2010 – All rights reserved
ISO 29581-2:2010(E)
Accuracy (trueness and precision) of measurement methods and results — Part 1:
General principles and definitions
ISO 2010 – All rights reserved
ISO 29581-2:2010(E)
ICS 91.100.10
Price based on 30 pages
ISO 2010 – All rights reserved
Source: http://www.gcs.gov.sa/SiteCollectionDocuments/ISO_29581-2_2010.pdf
Curriculum Vitae Israel Franco, MD, FAAP, FACS Licensure: New Jersey, 1989 Connecticut, 2004 Education: Albert Einstein College of Medicine 1300 Morris Park Ave., Bronx, NY 10461 August, 1979 - June, 1983 Degree: MD, June, 1983 New York University Washington Square South, New York, NY 10012
ACUPUNCTURE AND ACNE About acne Acne vulgaris, the most common type of acne, is a chronic inflammatory skin disease affecting hair follicles, and sebaceous glands and ducts. It occurs on the face in 99% of those affected and, less often, on the back and chest.(Layton 2010) Characteristic features include overproduction of sebum (seborrhoea); thickening of the follicle stratum corneum, which can lead to blockage and accumulation of sebum to form non-inflamed lesions called comedones; colonisation of the pilosebaceous ducts by Propionibacterium acnes; and inflamed lesions (e.g. papules, pustules, inflamed nodules, pus-filled cysts) that may be superficial or deep.(Layton 2010; Garner 2003) Scarring can result from abnormal wound healing following inflammatory damage.(Layton 2010) Acne conglobata is an uncommon and unusually severe form of acne characterised by burrowing and interconnecting abscesses and irregular scars.