Meganite.ca
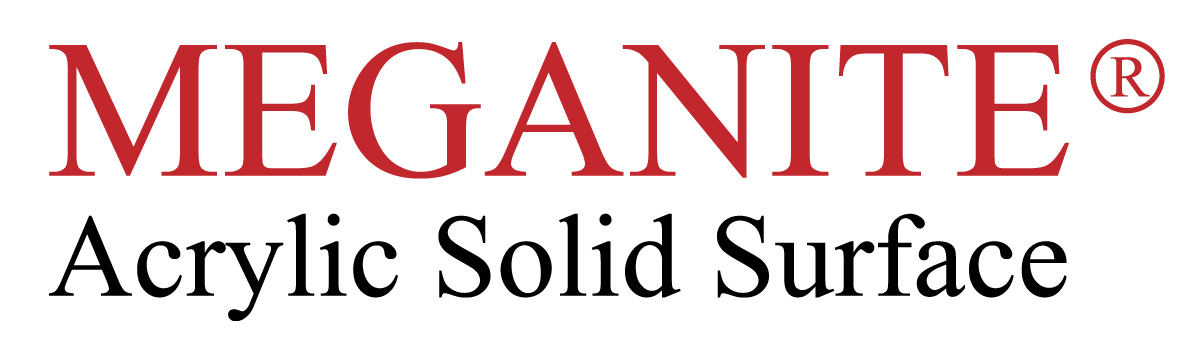
DISCLAIMER: All information in this PDF is produced and own by Integra Adhesives. MEGANITE is NOT RESPONSIBLE in any way for any claims as the result of providing this package. Please contact Integra Adhesives directly for all questions.
www.meganite.com
Adhesive Cross Reference Chart
Sheet Name
Sheet Code
Integra Alt Match
MEGANITE SURFACES
Pure White - 0190 *
MEGANITE SURFACES
MEGANITE SURFACES
White Chocolate - 0300
MEGANITE SURFACES
MEGANITE SURFACES
MEGANITE SURFACES
Antique White Granite
White Chocolate - 0300
MEGANITE SURFACES
White Chocolate - 0300
MEGANITE SURFACES
MEGANITE SURFACES
Bright White - 3011
MEGANITE SURFACES
Aztec Granite - 3028
MEGANITE SURFACES
MEGANITE SURFACES
Clay Brown - 2114 +
Warm Grey - 0290 *
MEGANITE SURFACES
MEGANITE SURFACES
Bright White - 3011
MEGANITE SURFACES
Biscayne Bay Granite
MEGANITE SURFACES
White Chocolate - 0300
MEGANITE SURFACES
Bright White - 3011
MEGANITE SURFACES
Stellar Grey - 2403
MEGANITE SURFACES
Blue Springs Boulder
MEGANITE SURFACES
Natural Almond - 0120
Bright White - 3011
MEGANITE SURFACES
MEGANITE SURFACES
MEGANITE SURFACES
Pure White - 0190
MEGANITE SURFACES
MEGANITE SURFACES
Butter Nut Granite
MEGANITE SURFACES
MEGANITE SURFACES
MEGANITE SURFACES
White Chocolate - 0300
MEGANITE SURFACES
Limestone - 2280
MEGANITE SURFACES
White Chocolate - 0300
Transparent White - 0271
MEGANITE SURFACES
Transparent Black - 0260
MEGANITE SURFACES
MEGANITE SURFACES
MEGANITE SURFACES
MEGANITE SURFACES
MEGANITE SURFACES
Warm Grey - 0290 *
MEGANITE SURFACES
MEGANITE SURFACES
Cocoa Brown - 0065 *
MEGANITE SURFACES
Bright White - 3011
MEGANITE SURFACES
Warm Grey - 0290
MEGANITE SURFACES
Dancing with the Stars
Arctic White - 3076
MEGANITE SURFACES
MEGANITE SURFACES
MEGANITE SURFACES
Desert Stone Granite
MEGANITE SURFACES
MEGANITE SURFACES
Oxford Brown - 2365
MEGANITE SURFACES
Transparent Black - 0260
Integra Adhesives Inc. (888) 862-6665 or (604) 850-1321
Color match may vary with manufacturers dye lot variations. Information is provided as a reference only; end user should verify suitability prior use.
Refer to MSDS for safety and handling information.
* Indicates tight seam required // + indicates custom colour (minimum orders may apply)
Adhesive Cross Reference Chart
Sheet Name
Sheet Code
Integra Alt Match
MEGANITE SURFACES
MEGANITE SURFACES
MEGANITE SURFACES
MEGANITE SURFACES
Transparent Black - 0260
MEGANITE SURFACES
Transparent Black - 0260
MEGANITE SURFACES
MEGANITE SURFACES
MEGANITE SURFACES
Give Peas a Chance
Aqueous - 3097 *
MEGANITE SURFACES
White Chocolate - 0300
MEGANITE SURFACES
MEGANITE SURFACES
Golden Meadow Granite
MEGANITE SURFACES
Goldrush Gemstone
Cocoa Brown - 0065
MEGANITE SURFACES
White Chocolate - 0300
MEGANITE SURFACES
Greenbrook Granite
MEGANITE SURFACES
Seafoam - 0220 *
MEGANITE SURFACES
Grey Glacier Granite
MEGANITE SURFACES
MEGANITE SURFACES
Hunter Green Granite
MEGANITE SURFACES
MEGANITE SURFACES
MEGANITE SURFACES
MEGANITE SURFACES
Transparent Black - 0260
MEGANITE SURFACES
MEGANITE SURFACES
Kaleidoscope Granite
MEGANITE SURFACES
MEGANITE SURFACES
Newgale Grey - 2340
MEGANITE SURFACES
Warm Grey - 0290
MEGANITE SURFACES
MEGANITE SURFACES
Nova Roca - 3049
MEGANITE SURFACES
Transparent White - 0271 *
MEGANITE SURFACES
MEGANITE SURFACES
Pudding Brown - 0181
MEGANITE SURFACES
MEGANITE SURFACES
Natural Almond - 0120
MEGANITE SURFACES
MEGANITE SURFACES
White Chocolate - 0300
MEGANITE SURFACES
Midnight Sky Mist
MEGANITE SURFACES
MEGANITE SURFACES
MEGANITE SURFACES
Tidal Sand - 0250
MEGANITE SURFACES
Absolute Grey - 2000
MEGANITE SURFACES
White Chocolate - 0300
MEGANITE SURFACES
Moonstone Granite
MEGANITE SURFACES
Tidal Sand - 0250
MEGANITE SURFACES
MEGANITE SURFACES
MEGANITE SURFACES
Integra Adhesives Inc. (888) 862-6665 or (604) 850-1321
Color match may vary with manufacturers dye lot variations. Information is provided as a reference only; end user should verify suitability prior use.
Refer to MSDS for safety and handling information.
* Indicates tight seam required // + indicates custom colour (minimum orders may apply)
Adhesive Cross Reference Chart
Sheet Name
Sheet Code
Integra Alt Match
MEGANITE SURFACES
Nova Roca - 3049
MEGANITE SURFACES
MEGANITE SURFACES
MEGANITE SURFACES
MEGANITE SURFACES
MEGANITE SURFACES
Natural Almond - 0120
MEGANITE SURFACES
Snow White - 0230
MEGANITE SURFACES
MEGANITE SURFACES
Parchment Granite
White Chocolate - 0300
MEGANITE SURFACES
MEGANITE SURFACES
Picnic in the Park
MEGANITE SURFACES
MEGANITE SURFACES
MEGANITE SURFACES
Transparent White - 0271
MEGANITE SURFACES
MEGANITE SURFACES
Mulberry - 3100 +
MEGANITE SURFACES
MEGANITE SURFACES
Quarrystone Granite
Warm Grey - 0290
MEGANITE SURFACES
Raspberry Granite
Dusty Rose - 0071
MEGANITE SURFACES
Transparent Black - 0260
MEGANITE SURFACES
Red Diamond Sparkle
Indus Red - 2240
MEGANITE SURFACES
Bright White - 3011
MEGANITE SURFACES
Brazilian Brown - 2100
MEGANITE SURFACES
Tidal Sand - 0250
MEGANITE SURFACES
Rocky Road Granite
MEGANITE SURFACES
MEGANITE SURFACES
Rose Garden Granite
MEGANITE SURFACES
MEGANITE SURFACES
Tidal Sand - 0250
MEGANITE SURFACES
Saddlebrown Granite
Pudding Brown - 0181
MEGANITE SURFACES
Butterscotch - 0050
MEGANITE SURFACES
MEGANITE SURFACES
Sandstone Granite
MEGANITE SURFACES
MEGANITE SURFACES
Red Pepper - 3051 +
MEGANITE SURFACES
Bright White - 3011
MEGANITE SURFACES
MEGANITE SURFACES
Shangri-la Boulder
Tidal Sand - 0250
MEGANITE SURFACES
MEGANITE SURFACES
White Chocolate - 0300
MEGANITE SURFACES
MEGANITE SURFACES
MEGANITE SURFACES
MEGANITE SURFACES
Soft White - 3050
MEGANITE SURFACES
MEGANITE SURFACES
MEGANITE SURFACES
South Beach Boulder
White Chocolate - 0300
Integra Adhesives Inc. (888) 862-6665 or (604) 850-1321
Color match may vary with manufacturers dye lot variations. Information is provided as a reference only; end user should verify suitability prior use.
Refer to MSDS for safety and handling information.
* Indicates tight seam required // + indicates custom colour (minimum orders may apply)
Adhesive Cross Reference Chart
Sheet Name
Sheet Code
Integra Alt Match
MEGANITE SURFACES
MEGANITE SURFACES
Pudding Brown - 0181
MEGANITE SURFACES
Staten Island Stone
MEGANITE SURFACES
MEGANITE SURFACES
MEGANITE SURFACES
Tiger Eye Gemstone
MEGANITE SURFACES
Paprika - 0140 *
MEGANITE SURFACES
Chameleon - 3008
MEGANITE SURFACES
Translucent Green
Chameleon - 3008
Crystal Clear - 1000 *
MEGANITE SURFACES
MEGANITE SURFACES
Under the Boardwalk
MEGANITE SURFACES
White Chocolate - 0300
MEGANITE SURFACES
Mercury Grey - 2300
MEGANITE SURFACES
MEGANITE SURFACES
MEGANITE SURFACES
White Crystal Boulder
Natural - 0130 *
MEGANITE SURFACES
White Mosaic Granite
Bright White - 3011
MEGANITE SURFACES
Newgale Grey - 2340
Natural Almond - 0120
MEGANITE SURFACES
Yellowstone Granite
MEGANITE SURFACES
Yorkshire Tan Granite
Tidal Sand - 0250
Integra Adhesives Inc. (888) 862-6665 or (604) 850-1321
Color match may vary with manufacturers dye lot variations. Information is provided as a reference only; end user should verify suitability prior use.
Refer to MSDS for safety and handling information.
* Indicates tight seam required // + indicates custom colour (minimum orders may apply)
The following information is provided as a basic guide to achieve accurate mix ratio proportioning
with dual component adhesives for Solid Surface and Engineered Stone. Tips and Techniques
Static mixers vary in mixing performance and pressure drop (back pressure) depending on the dimensions,
number of elements and the mixer design.
Use a static mixer with an adequate number of mixer elements and the lowest backpressure to minimize of ratio dispensing. Talk to your adhesive supplier as mixer design requirements vary depending on the
adhesive flow properties.
Partial y blocked static mixers or cartridge outlets can also have a negative effect on the cure. Check for crystallized or cured adhesive at the outlet before re-at aching a new tip to a previously used
cartridge. Dispensing guns:
Manual dispensing guns vary in mechanical advantage.
Higher mechanical advantage dispensers can produce more internal pressure. The higher the pressure the
more chance for of ratio dispensing. To minimize of ratio dispensing, use as lit le pressure as possible to dispense the adhesive and maintain a constant forward motion of the cartridge pistons.
Some dispensers have a non-drip feature that releases pressure at the end of each stroke. This is a useful
feature but it can add to off ratio dispensing if the gun is pumped and then paused between strokes. Apply a
technique of constant motion and a rapid re-grip of the trigger. Damaged or worn dispensing gun:
Damage to the ratchet / brake mechanism and cracks or missing teeth on the plunger of a dispensing gun
can cause uneven feeding of the pistons. Check the condition of the dispenser paying particular attention to
the ratchet mechanism. Look for broken teeth, build up of adhesive or play in the dispensing mechanism. Also look for loose, bent or missing piston rod ends.
Leaking cartridge pistons:
Check the condition of the dispenser. Look for excessive play in the piston rods or loose piston rod ends. Check cartridge position in the dispenser and ensure that it sits parallel to the piston rods. For pneumatic
systems, ensure there is a regulator on the dispenser providing control ed pressure. Adjust pressure to
provide adequate flow without overpowering the system. If leaking occurs, your supplier may wish to inspect the molded part for defects or damage as part of their quality control program.
Operator trigger action:
Some shops find that off ratio dispensing appears to be a random event and may occur more often with
some individual operators. The triggering action used with manual dispensers is an important technique to ensure an even cure.
Purge adhesive (1 tablespoon) immediately start to dispense adhesive. Apply smooth even strokes;
maintain constant feed and pressure using the ful stroke of the trigger. Do not stop and let adhesive drool out of the tip between strokes, quickly re-trigger the gun and continue until dispensing is completed. To
minimize of ratio dispensing, use as lit le pressure as possible to dispense the adhesive and maintain a
constant forward motion of the cartridge pistons. Cold Adhesive: Adhesive stored in the fridge or a cold shop, should be al owed to return to room temperature before use.
Some adhesive components become thicker at low temperatures and may not mix as wel . Thickened material creates higher pressure in the cartridge and tip. Higher pressure wil flex the cartridge wall and can
throw of mix ratio. If you re-warm adhesive, make sure the cartridge plug is in place. A previously used
mixing tip left on the cartridge can al ow expanding adhesive to back flow into the activator chamber and result in a plugged cartridge.
Never warm adhesive above 110 degrees f. The activator may be damaged.
Cold Sheet material:
Bonding sheet goods that have been stored below normal room temperature wil cause the adhesive to cure
slowly in the joint. Fabricating with cold sheet goods may prevent a ful cure from developing in areas with
lower than optimum activator levels. Warm room air wil cause the adhesive on the surface to cure much faster than the adhesive in the joint
where the cold substrate will absorb much of the energy from the chemical reaction. This can cause joints to
have low strength. For best results, al ow product being joined to reach a room temperature of 60 f before assembly.
Disturbing adhesive prior to cure:
Disturbing the exposed adhesive at the joint line prior to the surface curing can cause the adhesive to remain sticky and under cured at the surface.
Let the adhesive cure undisturbed until the surface dul s and becomes hard. Do not handle the project until
there is suf icient bond strength. A rough estimate for handling time (materials that are at room temperature when bonded) is 2 X working time. i.e. 15 minute to set up; al ow 30 minutes before applying stress to the
For optimum shelf life and performance, store adhesive upright away from direct sunlight in a cool area or
It is possible that an air bubble could be trapped in the activator or adhesive, gases can also form in the activator if it is subjected to high temperatures during storage or shipping.
In the event that a gas or air bubble was trapped in the cartridge, upright storage should allow it to reach the
top (outlet) of cartridge to be eliminated during the initial purge.
Activator failure:
Activator exposed to high temperatures during transport or storage wil start to break down and loose
strength, this wil general y show up as a slower cure. High temperature decomposition of the activator can also release gasses into the activator component.
Bubbles may appear in the dispensed product and the compressibility of the gases may act like a spring
compressing with each pul of the trigger, producing fluctuations in the dispensing rate, off ratio cure and drooling at the tip.
Our tests revealed that some manufacturers activator may separate after freezing; this can cause the
proportions of active ingredients (therefore the cure) to vary. If you suspect damaged activator, contact your supplier.
With al of the variables involved in manual and pneumatic dispensing of dual component adhesives, it is impossible to completely eliminate the possibility of any variation in mix ratio. However if you purchase
quality adhesives, store them correctly and fol ow these few simple procedures you can expect a near
perfect seam every time. We also recommended that you run two smal beads instead of one larger single bead. The overlapping of adhesive streams wil greatly reduce the possibility of under cured areas in any
Thanks for taking the time to review this info sheet. It is not intended as a complete guide to meter mix and dispense systems but was compiled from many years of hands on experience.
If you have any questions, comments or spot ed something we missed, please contact the writer.
Douglas Turner [email protected]
Integra Adhesives Inc. May 18, 2004
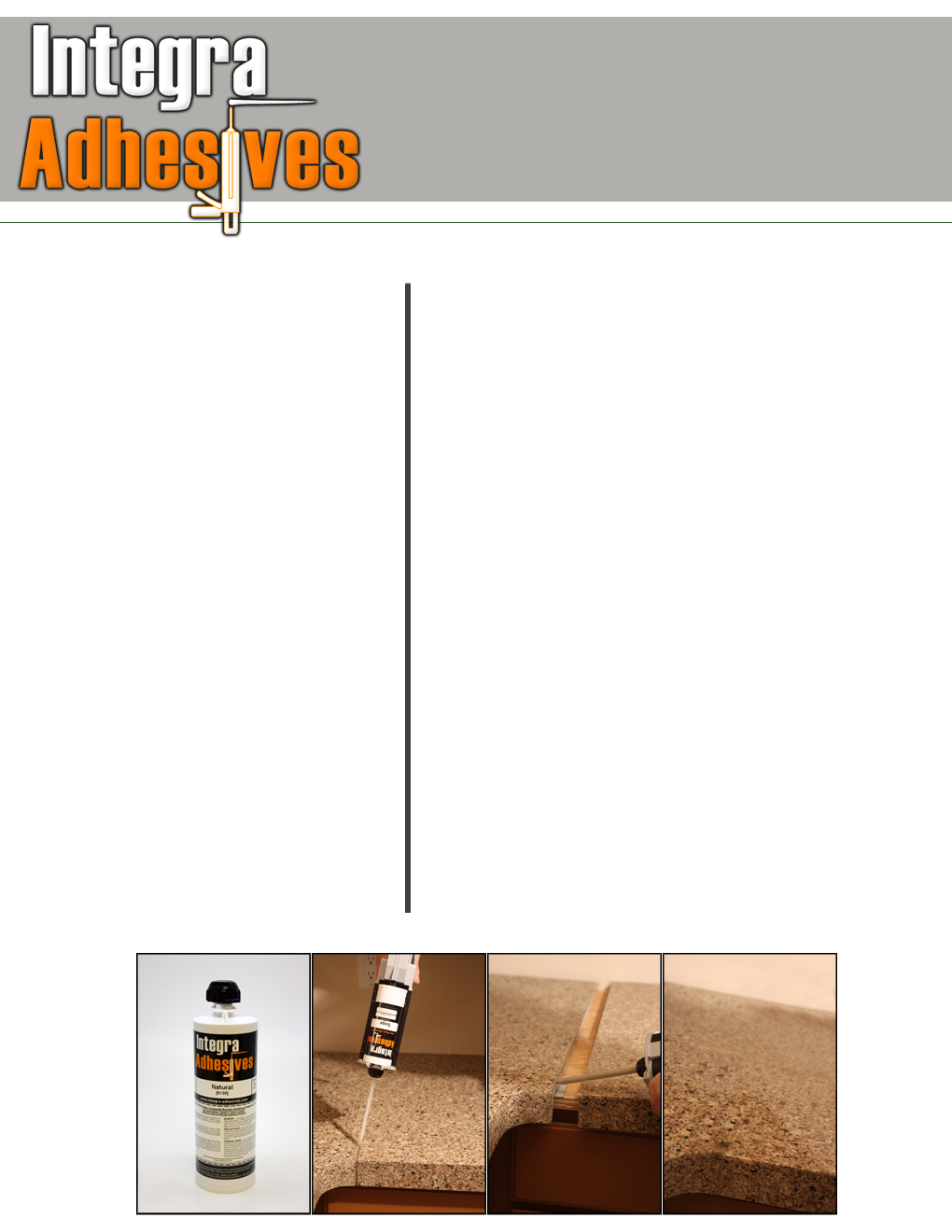
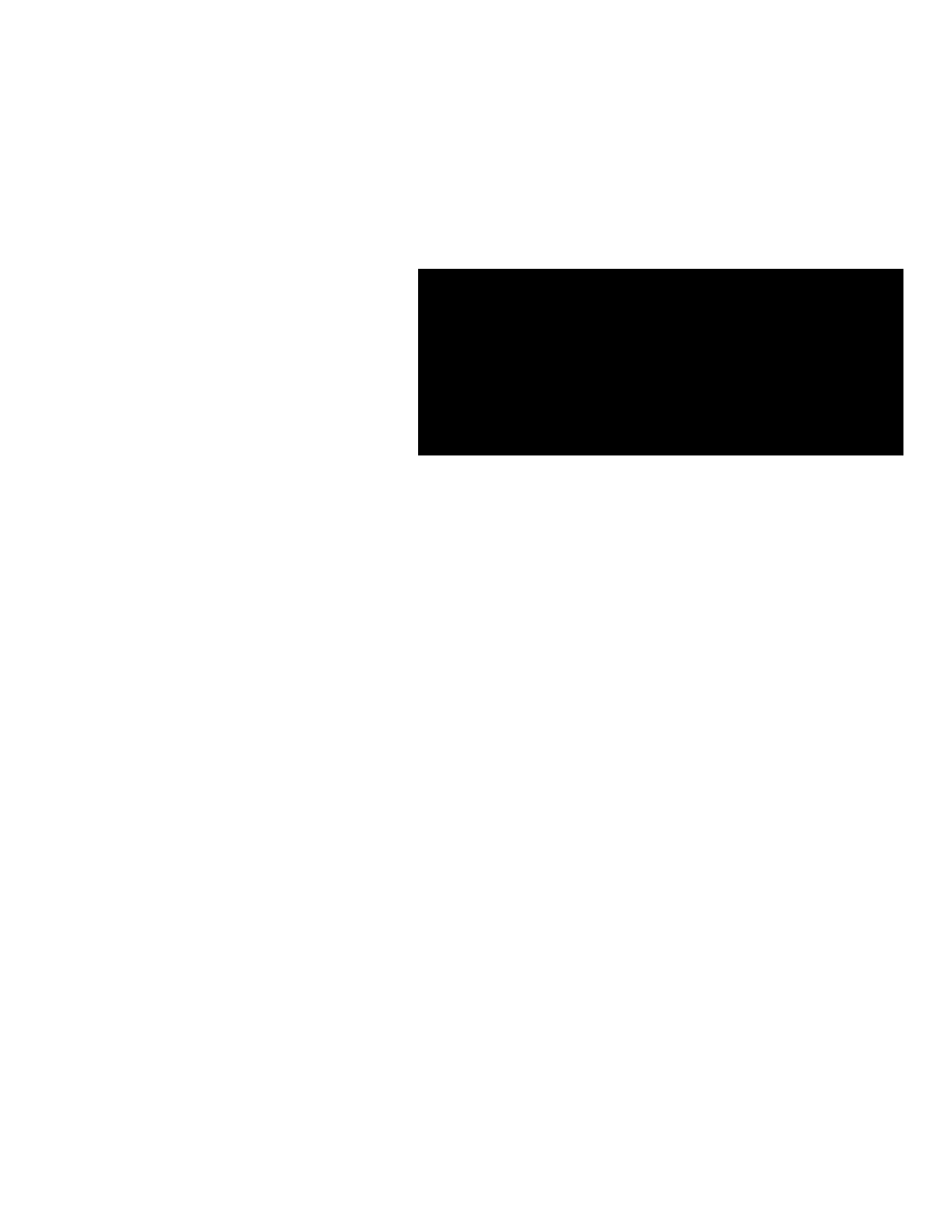
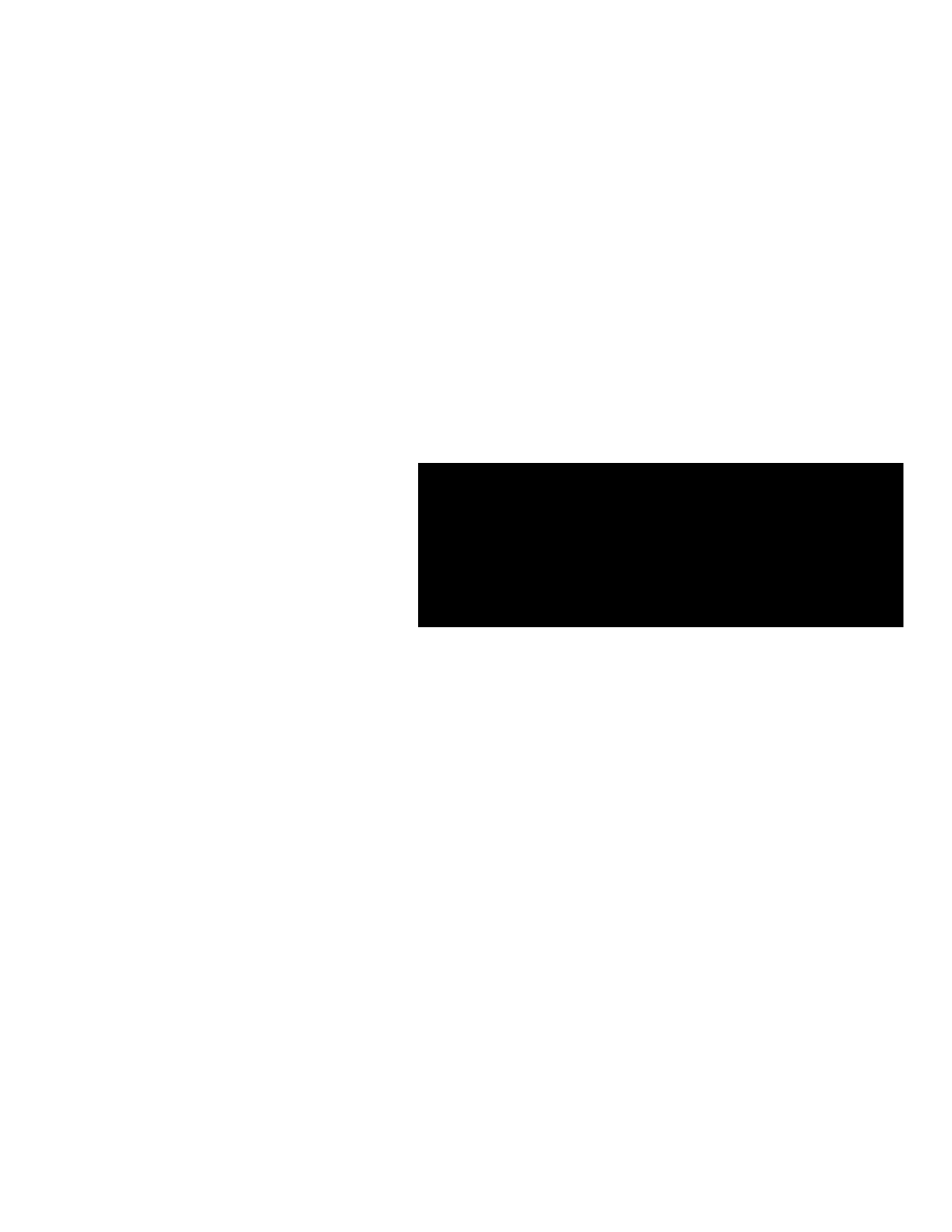
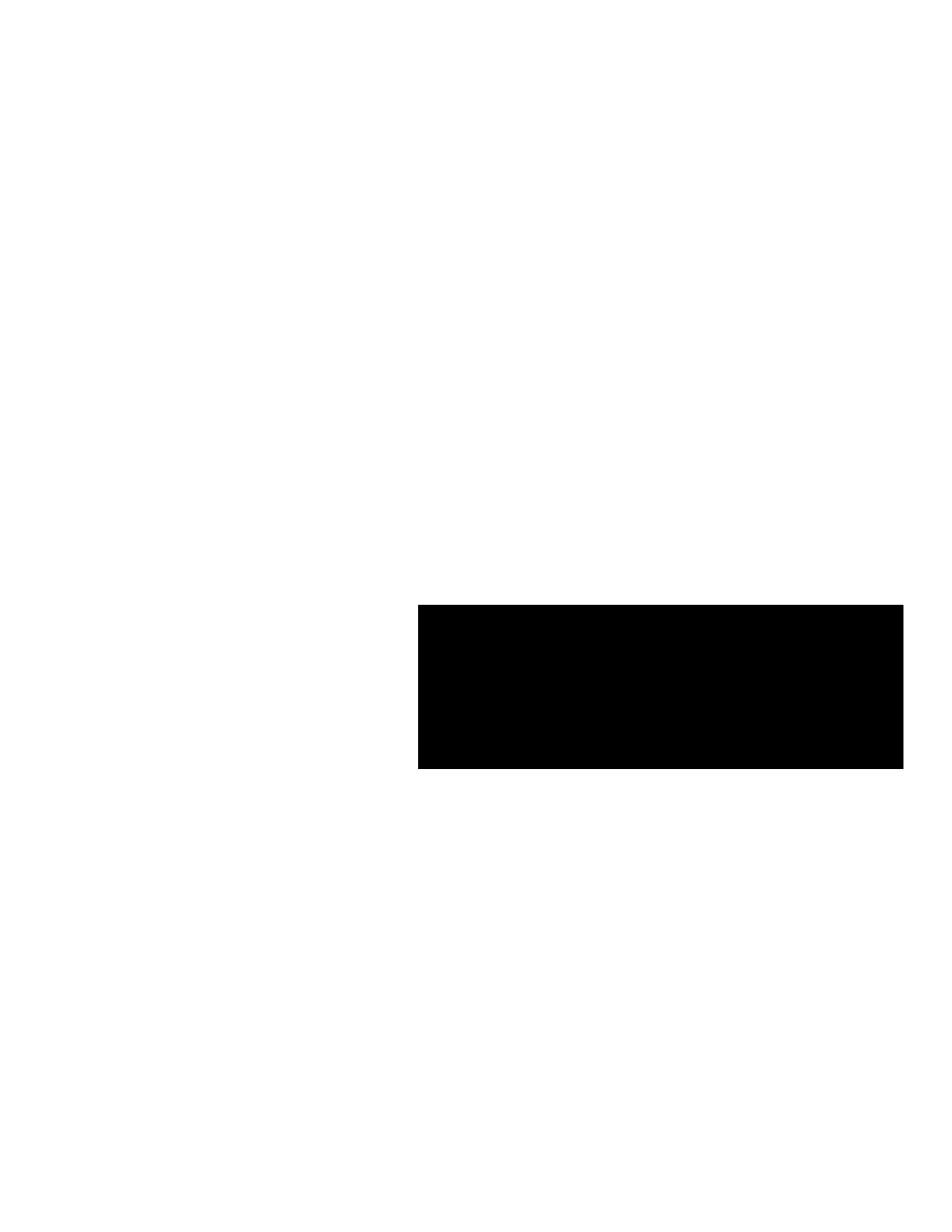
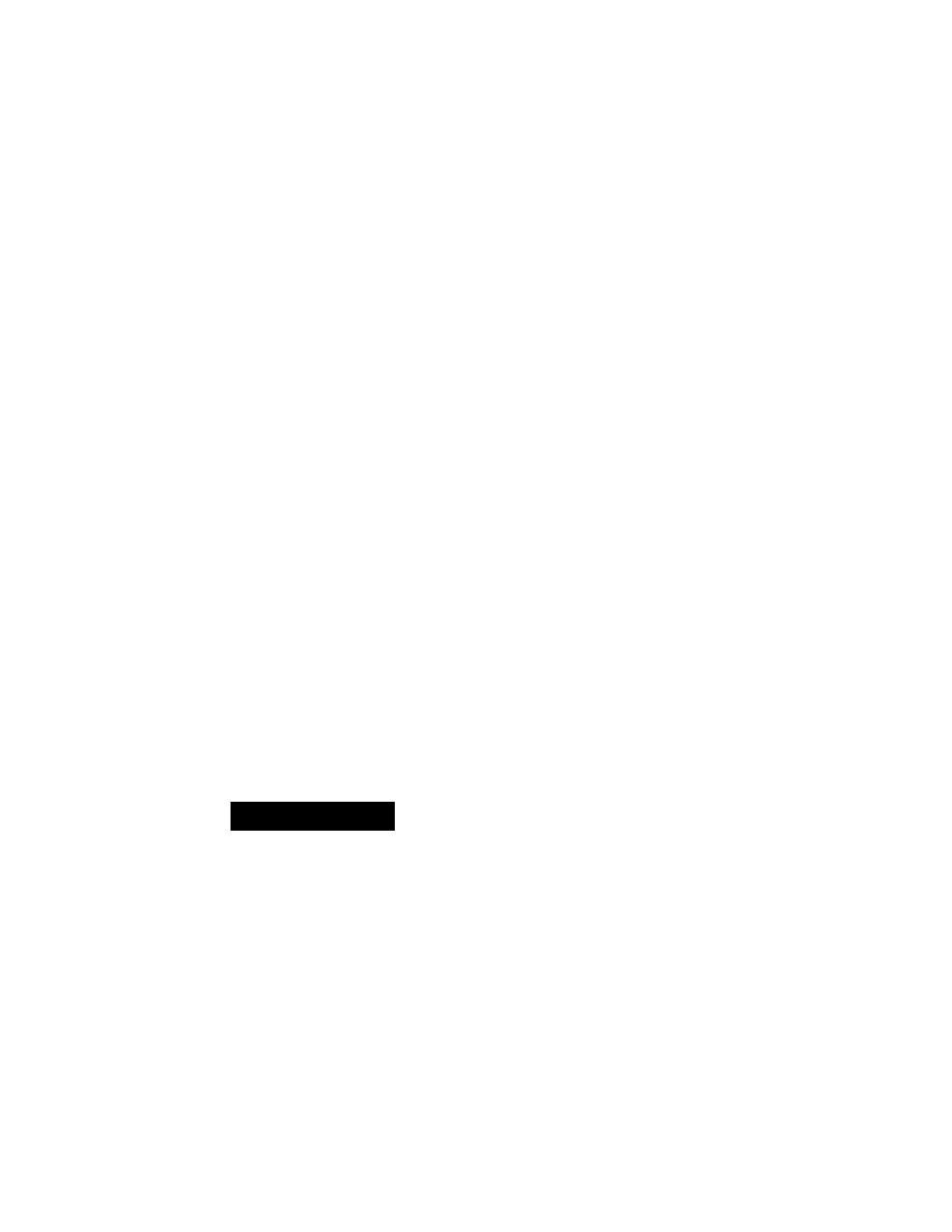
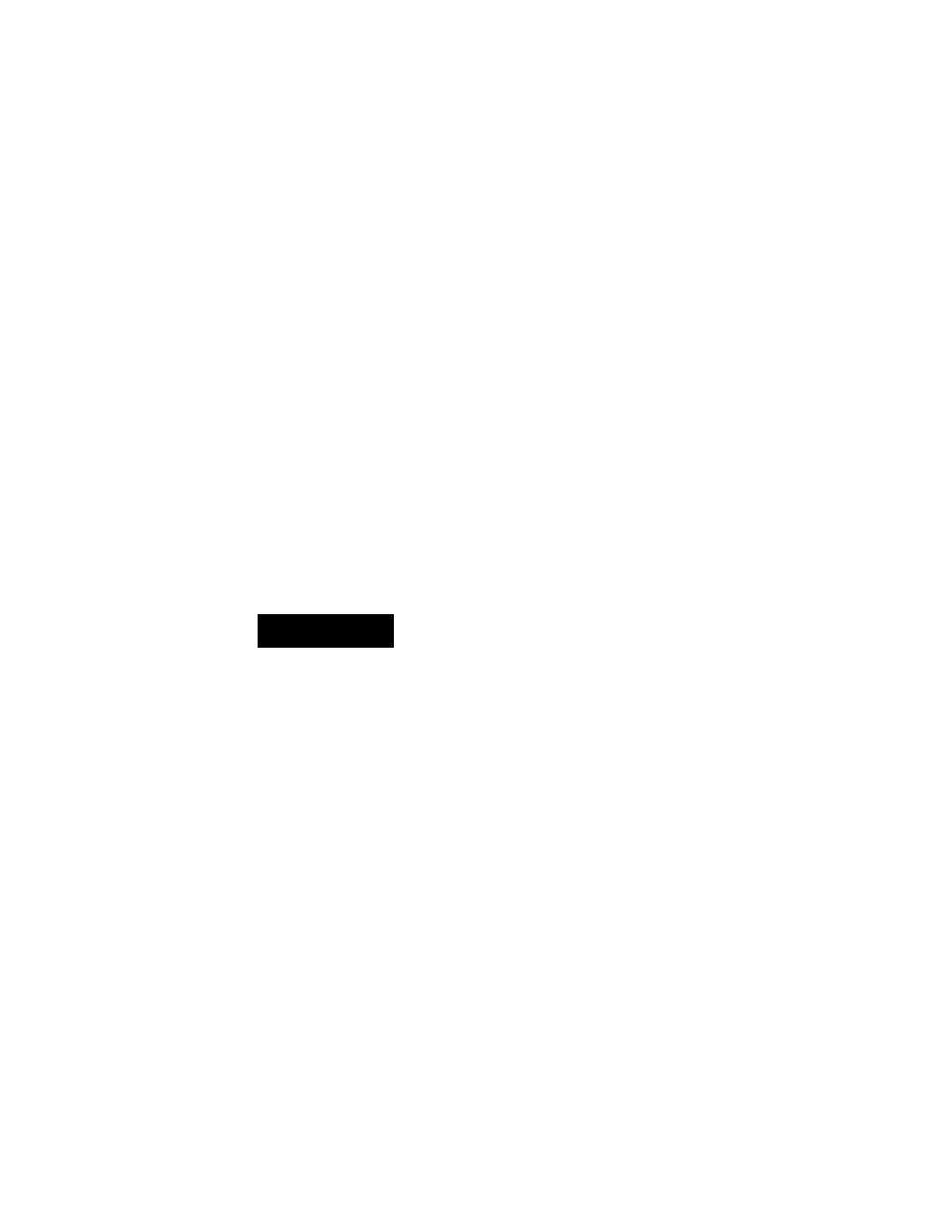
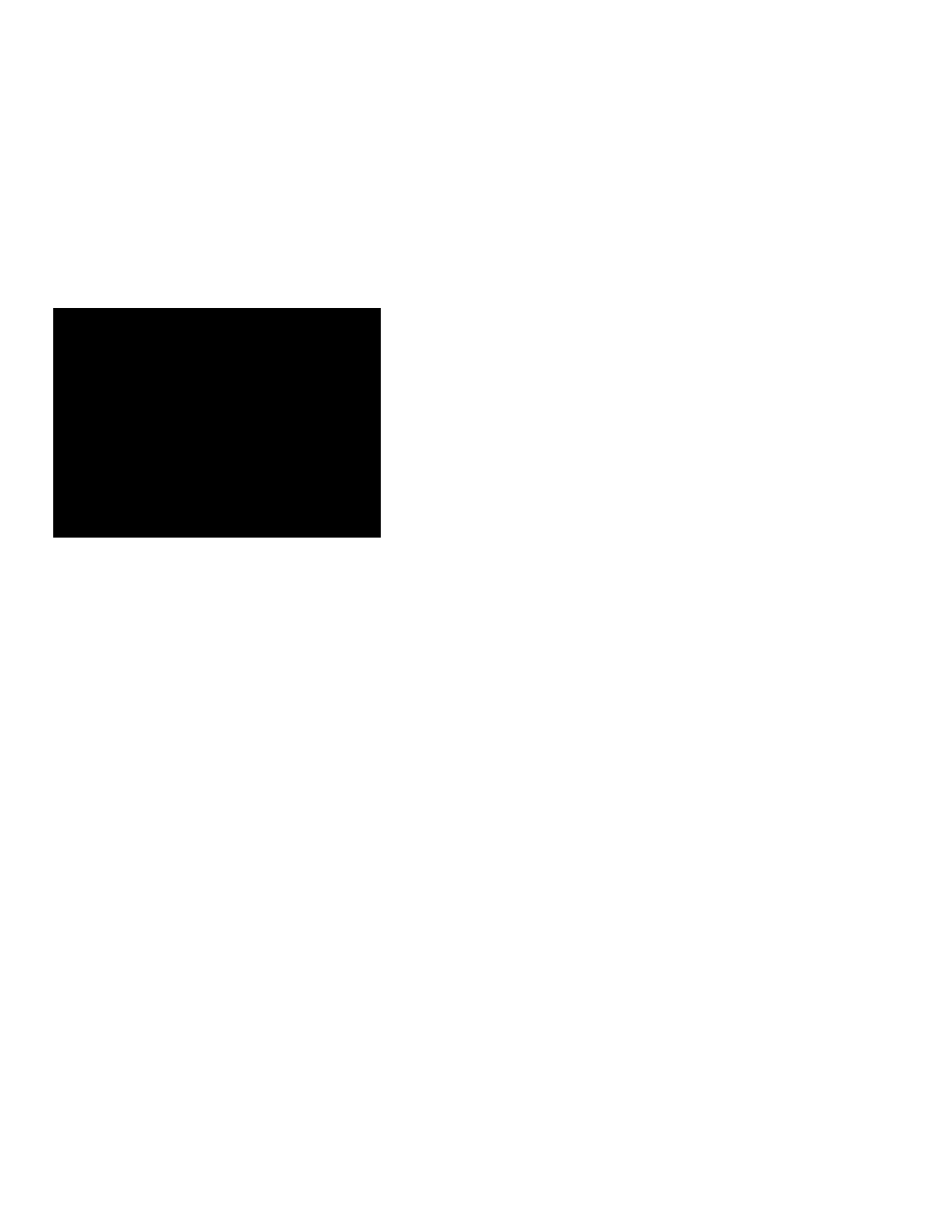
Colour Matching
Integra is known industry wide for it's excellence in matching colours. The lab uses a combination of
new colour technology and years of experience to produce unrivalled colour matches for every surface.
Cross reference charts
sheet manufacturers and changing trends in the Natural stone industry. While most surfaces can be
matched using the top 20-30 adhesive colours, Integra customers have access to a pallet of over 200
colours. Beyond that custom colours can be formulated upon request.
Dispensing / Packaging
Surface Bonder Xi is packaged in dual component cartridges as part of a meter/mix/dispense sys-
tem utilizing specialized dispensing guns and static mixing tips. Surface Bonder Xi is available in
100ml, 250ml, and 500ml cartridges in many colours matching Solid Surfaces, Engineered Stone,
Granite and Quartz Surfaces.
The 100ml cartridge is complimented by Integra's 100ml Dispensing Gun and Integra X-Stream Static Mixers.
The 250ml cartridge is complimented by Integra's 250ml Dispensing Gun and Integra X-Stream Static Mixers. The 500ml cartridge is complimented by Integra's 500ml Dispensing Gun and Integra X-Stream Static Mixers.
Case sizes100ml Cartridge = 20 Cartridges250ml Cartridge = 20 Cartridges500ml Cartridge = 12 Cartridges
Shipping Options
Integra's adhesives are stocked at several locations in North America and Europe. A 2 to 3 day lead
time can generally be expected for ground delivery within the continental US and Canada.
Flammable adhesives require specialized packaging and documentation for air transport.
Please contact Integra for information on overnight air shipping.
Order Processing-North America
Order Processing - European Union
Orders processed by email, fax or phone.
Orders processed by email, fax or phone.
Integra Main number 1 (604) 850-1321
Integra International Phone 1 (604) 850-1321
Toll free 1 (800) 862-6665
Integra International Fax 1 (604) 850-1354
Fax 1 (604) 850-1354
Distributor Information - Please contact us for the names and location of distributors in your area.
Performance Characteristics– Surface Bonder Xi
Appearance - Component A
Clear or coloured - viscous liquid
Appearance - Component B
Clear to white - viscous liquid
35,000 - 150,000 CPS
20,000 - 25,000 CPS
S.G. Combined (Density)
Recommended Bond Line
0.002 - 0.040 inch / 0.5 - 1.0mm
Bond Strength (Solid Surface)
4000 - 6000 PSI / 280 - 420 kg/cm²Flexural Strength (ASTM D-790)
Bond Strength (Quartz Surfaces)
3000 - 4000 PSI / 210 - 281 kg/cm²Flexural Strength (ASTM D-790)
Impact Resistance ISSFA method
Stain Resistance ISSFA method
Water Resistance ISSFA method
Heat Resistance ISSFA method
UV Stability ISSFA method
Shelf Life Component A
Shelf Life Component B
1 year (Temperature Dependent)
Mix Ratio (Volume) A/B
Storage and handling:
the appropriate Material Safety Data Sheet. Information is supplied at time of initial purchase and may be requested from the manufac-turer or downloaded from the web sight at- www.integra-adhesives.com Store the adhesive in a cool area away from direct sunlight. High temperatures will reduce the shelf life of the adhesive and activator. Exposure of activators, including cartridges, which contain activators, above 100 F. rapidly diminishes the product's reactivity and must be avoided. Refrigeration is an acceptable means to increase storage life, however freezing should be prevented. Shelf life results are based on constant temperature storage between 55 and 75 f - (12/23 c).
Dispensing:
Integra adhesives are supplied in kit form at the appropriate mix ratio. Always maintain this ratio when mixing. Excess activator will cause
higher than normal exothermic temperatures. Avoid mixing large quantities or creating thick cross sections (over 1/4 inch) as high tem-
peratures may cause damage, skin burns and create the release of volatile vapors. To assure maximum bond strength, surfaces must be
All adhesive application and part positioning should occur before the working time of the mix has expired. After indicated working time,
Clean-up is easiest before the adhesive has cured. If the adhesive is already cured, careful scraping, followed by a solvent wipe may be the most effective method of clean up.
Working time:
The working time information is provided as an estimate of the time between mixing and set up of the adhesive. The working time is
effected by the mixing ratio, air temperature, adhesive temperature, and the substrate temperature as well as the shelf life condition of
the adhesive. For best results, use the adhesive at temperatures between 60 and 85 f. - (15/30 c). High temperatures increase the cure
rate while lower temperatures slow the cure. Use at temperatures below 55 f - (12 c). may cause incomplete cure.
Disclaimer:
The Information provided, is based on laboratory testing under controlled conditions. It is the responsibility of the end user to test the
adhesive on the intended substrates under the conditions which they will be used, and to determine the suitability of the adhesive for
the intended purpose. Integra Adhesives makes no representations or warranties of any kind with respect to the data on this form or the
Adhesive Kits
SAFETY DATA SHEET
This Safety Data Sheet complies with the Canadian Controlled Product Regulations and
with the requirements of 29 CFR § 1910.1200
1. Product and Supplier Identification
Products: Surface Bonder Xi, RPT-01, Trim Bonder TR30/TR40
Rodding Compound RD50, Sink Bonder SK11
Product Use: Bonding agent for acrylic composite, polyester composite, quartz composite, natural stone,
FRP/GRP and steel reinforcing rods
Manufacturer: Integra Adhesives Inc.,
Unit 4, 33759 Morey Avenue Abbotsford, BC, Canada, V2S 2W5 Telephone: +1(604) 850-1321 Facsimile: +1(604) 850-1354 Emergency Telephone Number: +1(604) 986-4617
Supplier:
2. Composition
Component
Exposure Limits
Methyl Methacrylate
ACGIH1 TLV-TWA: 50 ppm
Carcinogen A4, Sensitizer
ACGIH STEL: 100 ppm
Inert Ingredients or those
below disclosure requirements
Component
Exposure Limits
Benzoyl Peroxide2
ACGIH1 TLV: 5 mg/m3
Tricresyl Phosphate
ACGIH1 TLV: 0.1 mg/m3
CAS No 1330-78-5
Reaction product of
Epichlorohydrin and
Skin and respiratory sensitizer
CAS No 25085-99-8 Inert Ingredients or those
below disclosure requirements
Integra Adhesives Inc.,
September 3, 2010
Adhesive Kits
ABBREVIATION KEY: N/p: not published, N/d: not determined, N/ap: not applicable, N/av: not available
Exposure limits may vary from time to time and from one jurisdiction to another. Check with local
regulatory agency for the exposure limits in your area.
ACGIH: American Conference of Environmental Industrial Hygienists
Part B does not meet the requirements for inclusion in Class 5.2 under Part 2.5.3.2.1 of the thirteenth revise edition of the Recommendations on the Transport of Dangerous Goods, Model Regulations.
3. Hazards Identification
Routes of Entry:
Skin Contact: Yes(Part A)
Eye Contact: Yes (Part B)
Ingestion: Yes (Part A)
Inhalation: Yes (Part A)
Emergency Overview: Methyl methacrylate is extremely volatile and can form high concentration of
vapours at room temperature. Being heavier than air, it may spread long distances and sources of ignition
may cause flashbacks to source. Liquid may float on water spreading fire. This product is a confined space
hazard. Closed container may rupture when exposed to heat or to sunlight. High vapour concentrations may
cause headache, nausea, dizziness, drowsiness, confusion and incoordination. Very high concentrations
may cause loss of consciousness and death. Skin sensitizer! May cause severe allergic skin reactions.
Acute Health Effects:
Inhalation: This product contains materials that are extremely volatile. Low concentrations probably
irritating to the nose, throat and respiratory tract. Higher concentrations can probably cause symptoms of
central nervous system depression, such as headache, nausea dizziness, drowsiness, and confusion.
Extremely high concentrations can cause loss of consciousness and death. Dues to its irritating nature,
methyl methacrylate may cause fluid build up in lungs. Symptoms are shortness of breath, pain in chest and
difficultty breathing. Symptoms may be delayed up to 24 hours.
Skin Contact: This product is mildly irritating to the skin, but exposure is considered major due to its ability
to sensitize the skin.
Eye Contact: Ingredients in Part B may cause severe eye irritation.
Ingestion: Ingestion may cause effects similar to those experienced under the heading "INHALATION"
Chronic Health Effects:
In most exposure situation, prolonged exposure may cause central nervous system depression. In addition,
prolonged inhalation exposure may cause bronchitis which includes coughing. This product is a skin
sensitizer (methyl methacrylate) and may be a respiratory sensitizer based on limited studies (reaction
product of epichlorohydrin and bisphenol A). One sensitized to this material, even a small additional
exposure will produce severe allergic reactions such as rash, itching, and swelling. This material cannot be
classified by IARC as a carcinogen to humans.
Medical Conditions Aggravated by Exposure:
Pre-existing eye, skin, respiratory tract disorders may be aggravated by exposure.
4. First Aid Measures
Inhalation: This product is flammable. Take proper precautions. Remove victim to fresh air. Give artificial
respiration if indicated. Get medical attention.
Skin Contact: Avoid direct contact. Wear chemical protective clothing, if necessary. Quickly and gently
blot or brush away excess chemical. Wash gently and thoroughly with water and non-abrasive soap for 20
minutes or until chemical is removed. Under running water, remove contaminated clothing, shoes and
leather goods (e.g. watchbands, belts). Completely decontaminate clothing, shoes and leather goods before
Integra Adhesives Inc.,
September 3, 2010
Adhesive Kits
re-use or discard. If the contact is severe and pain persists after long term rinsing with water, rinse the
contaminated area with lukewarm pasteurized milk. After pain has stopped, rinse thoroughly with water.
Obtain medical attention immediately.
Eye Contact: MAY CAUSE EYE IRRITATION. Check and remove any contact lenses. Flush with plenty of
water for at least 20 minutes, occasionally lifting the upper and lower eyelids. DO NOT INTERUPT
FLUSHING. Take care not to contaminate non-affected eye. Seek medical attention.
Ingestion: If patient is conscious, give three or four glasses of water. Do not induce vomiting Do not give
anything by mouth to a convulsing or unconscious person. Get medical attention.
General Comments: Good personal hygiene is essential. Avoid eating, smoking or drinking in work
areas.
5. Fire Fighting Measures
Part A
Flash point:
9oC TCC (Methyl Methacrylate)
Autoignition Temperature:
435oC. See information under "Fire Fighting Instructions"
Lower Explosive Limit:
Upper Explosion Limit:
Sensitivity to Impact:
Sensitivity to Static Discharge:
Part B
Flash point:
Autoignition Temperature:
Lower Explosive Limit:
Upper Explosion Limit:
Sensitivity to Impact:
Sensitivity to Static Discharge:
Hazardous Combustion Products: Burning may produce oxides of carbon.
Extinguishing Media: Use carbon dioxide, alcohol foam, or dry chemical. Water should be used to cool
surrounding containers.
Fire Fighting Instructions: Vapour will flash and the liquid will burn. Keep away from al sources of
ignition and avoid elevated temperatures. Vapours are heavier than air, and may collect in low-lying areas.
Firefighters must wear self-contained breathing apparatus and full protective clothing.
6. Accidental Release Measures
Personal Protection: Wear adequate personal protection to prevent skin contact. See Section 8 for
specific recommendations.
Environmental Precautions: Prevent release into waterways and sewers. Stop spil as soon as possible
to prevent contamination of soil, groundwater, or surface water.
Cleanup Procedures: Toxic, flammable liquid, insoluble or very slightly soluble in water. Keep away from
heat. Keep away from sources of ignition. Stop leak if without risk. Absorb with DRY earth, sand, or other
non-combustible material. Prevent entry into sewers, basements, or confined areas. Dike if needed.
Eliminate al sources of ignition. Call for assistance on disposal. Consult national, provincial, and local
regulations.
7. Handling and Storage
Integra Adhesives Inc.,
September 3, 2010
Adhesive Kits
Handling Procedures: Keep away from heat and al sources of ignition. Ground all equipment containing
material. Do not ingest. Do not breathe gas, fumes, vapor, or spray. Follow safe work procedures and wear
appropriate personal protective equipment.
Storage: Keep well away from al sources of ignition. Store in a cool well-ventilated area out of direct
sunlight and away from heat and ignitions sources. Do not store near foodstuffs. Methyl Methacrylate should
not be stored for longer than 3 months. Containers should be checked weekly after 30 days to determine
inhibitor concentration and possible polymerization. Store away from oxidizers and corrosives and other
incompatible materials such as sulfuric acid, peroxides, alkali metal, which increase the risk of fire and
explosion.
8. Exposure Controls, Personal Protection
Occupational Controls: ACGIH TLV-TWA: 50 ppm, Sensitizer (methyl methacrylate)
Engineering Controls: If used indoors, ensure adequate non-sparking ventilation. Remove all sources of
ignition and post "No Smoking" signs in the work place. Keep away from heat, and never weld, cut, or solder
empty containers. Use adequate ventilation to reduce concentration to below TLV.
Respiratory Protection: NIOSH RECOMMENDATIONS FOR METHYL METHACRYLATE
CONCENTRATIONS IN AIR:
UP TO 1000 ppm: SAR operated in a continuous-flow mode*; or full-facepiece chemical cartridge respirator
with organic vapour cartridge(s); or gas mask with organic vapour canister; or powered air-purifying
respirator with organic vapour cartridge(s)*; or full-facepiece SCBA; or ful -facepiece SAR.
EMERGENCY OR PLANNED ENTRY INTO UNKNOWN CONCENTRATIONS OR IDLH CONDITIONS:
Positive pressure, full-facepiece SCBA; or positive pressure, full-facepiece SAR with an auxiliary positive
pressure SCBA.
ESCAPE: Gas mask with organic vapour canister; or escape-type SCBA.
*NOTE: Substance causes eye irritation or damage; eye protection needed.
Skin Protection: Guidelines for methyl methacrylate:
RECOMMENDED (resistance to breakthrough longer than 8 hours): Tychem(TM) F, Tychem(TM) BR/LV,
Tychem(TM) Responder(TM), Tychem(TM) TK.
CAUTION, use for short periods only (resistance to breakthrough within 1 to 4 hours): Butyl rubber, Polyvinyl
alcohol, Viton(TM)/Butyl rubber.
NOT RECOMMENDED for use (resistance to breakthrough less than 1 hour): Natural rubber, neoprene
rubber, nitrile rubber, polyvinyl chloride, Viton(TM).
Recommendations are NOT valid for very thin Natural rubber, Neoprene, Nitrile and PVC gloves (0.3 mm or
less).
Resistance of materials can vary from product to product. Breakthrough times are obtained under conditions
of continuous contact, general y at room temperature. Evaluate resistance under conditions of use and
maintain clothing carefully.
Eye and Face Protection: Use chemical safety goggles.
Footwear: As recommended by worksite.
Other: Eyewash and showers should be located near work areas.
9. Physical and Chemical Properties
Integra Adhesives Inc.,
September 3, 2010
Adhesive Kits
Part A
Appearance:
Clear transparent
Melting Point:
liquid, may be tinted
Boiling Point:
Freezing Point:
Relative Density:
Vapour Pressure:
Solubility:
Slightly soluble in cold
Partition Coefficient: No data
Evaporation Rate:
Vapour Density:
Heavier than air
Part B
Appearance:
Boiling Point:
Freezing Point:
Relative Density:
Vapour Pressure:
Solubility:
Slight solubility
Partition Coefficient: No data
Vapour Density:
Evaporation Rate:
Melting Point:
10. Stability and Reactivity
Chemical Stability: This product is stable.
Hazardous Polymerization: May polymerize violently with risk of fire and explosion. Uninhibited methyl
methacrylate with low inhibitor concentration, polymerizes slowly at room temperature and on exposure to
light and air, and readily at elevated temperatures, greater than 65˚C (149˚F). Polymerization becomes self-
sustaining above 95 deg C. Metal salts (e.g. ferric or aluminum chloride), peroxides, oxidizers and strong
acids may also cause polymerization.
Incompatibility: Oxygen, oxidizing agents - Increased risk of fire and explosion. Can form explosive
peroxides. Strong acids (e.g. sulfuric acid, oleum, chlorosulfonic acid) – Increased temperature and
pressure; increased risk of fire and explosion. Alkali metal, graphite compounds, metallic halide salts,
peroxides (dibenzoyl peroxide di-tertbutyl peroxide), azoisobutyronitrile – Can initiate polymerization.
Byllithium - Explosion can occur. Halogens - Can react with low concentrations of halogens, in the presence
of UV light, to form a strong irritant. Can form peroxides in the presence of light and air or on contact with
acids. Methyl Methacrylate has been involved in several plant-scale explosions when stored inappropriately
or accidentally heated.
Part B is an organic peroxide listed as an incompatible substance to Part A. Mixing Part A and B must be
done under control ed condiditons as prescribed in the product directions. Use of the resin dispensers
provided with the resin kits are adequate for measuing correct amounts of each.
Hazardous Decomposition Products: Various oxides of carbon and unidentified compounds in
smoke.
11. Toxicological Information
Acute Exposure (LD50):
Acute Exposure (LC50):
Chronic Exposure:
Exposure Limits:
Irritancy:
Part A (methyl methacrylate) is a skin sensitizer. See Section 3.
Part B (reaction product of epichlorohydrin and bisphenol A) may
be a respiratory sensitizer based on limited studies.
None observed other than central nervous system depression
No ingredients listed by IARC
Integra Adhesives Inc.,
September 3, 2010
Adhesive Kits
Reproductive Toxicity:
No evidence reported
No evidence reported
Synergistic Products:
Methyl methacrylate metabolism is slowed down by the presence of other organic solvents, including ethyl alcohol.
12. Ecological Information
Environmental Toxicity:
Methyl methacrylate:
TLm Pimephales promelas (fathead minnow) 499-159 mg/l/24-96 hr /Conditions of bioassay not specified TLm Lepomis macrochirus (bluegill) 368-232 mg/l/24-96 hr /Conditions of bioassay not specified TLm Carassius auratus (goldfish) 423-277 mg/l/24-96 hr /Conditions of bioassay not specified TLm Lebistes reticulatus (guppies) 368 mg/l/24-96 hr /Conditions of bioassay not specified Toxicity threshold (cell multiplication inhibition test): Pseudomonas putida (bacteria): 100 mg/l
Benzoyl peroxide:
No data available.
Tricresyl Phosphate:
LC50 Rainbow trout (weight 0.2 g) 260 ug/l/96 hr (95% confidence interval 210-322 ug/l), flow-through test at 12 deg C.
LC50 Channel catfish (weight 1.3 g) 803 ug/l/96 hr (95% confidence interval 672-959 ug/l),
flow-through test at 12 deg C.
LC50 Bluegil (weight 0.6 g) 150 ug/l/96 hr (95% confidence interval 102-220 ug/l), flow-through test at 12 deg C.
LC50 Yellow perch (weight 0.7 g) 502 ug/l/96 hr (95% confidence interval 384-656 ug/l),
flow-through test at 12 deg C.
Environmental Fate:
Methyl methacrylate:
TERRESTRIAL FATE: Based on a classification scheme, a Koc value of 95 indicates that methyl methacrylate is expected to have high mobility in soil. Volatilization of methyl methacrylate from moist soil surfaces is expected to be an important fate process given an estimated Henry's Law constant of 3.2X10-4 atm-cu m/mole, from its vapor pressure of 38.5 mm Hg and water solubility of 1.6X10+4. The potential for volatilization of methyl methacrylate from dry soil surfaces may exist based upon its vapor pressure. Screening tests indicate that methyl methacrylate is readily biodegradable; it reached 94% of its theoretical BOD in 2 weeks using an activated sludge inoculum.
AQUATIC FATE: Based on a classification scheme(1), a Koc value of 95 indicates that methyl methacrylate is not expected to adsorb to suspended solids and sediment in water. Volatilization from water surfaces is expected based upon an estimated Henry's Law constant of 3.2X10-4 atm-cu m/mole, from its vapor pressure of 38.5 mm Hg and water solubility of 1.6X10+4. Volatilization half-lives for a model river and model lake are 6 hours and 5 days, respectively, using an estimation method. Hydrolysis of methyl methacrylate may be a significant process under basic conditions based upon a hydrolytic half-life of 3.4 hours at pH 11; half-lives of 4 years, 140 days, and 14 days were determined at pH 7, 8, and 9, respectively. According to a classification scheme, an estimated BCF of 7, from a
Integra Adhesives Inc.,
September 3, 2010
Adhesive Kits
log Kow of 1.38, suggests the potential for bioconcentration in aquatic organisms is low. Screening tests indicate that methyl methacrylate is readily biodegradable; it reached 94% of its theoretical BOD in 2 weeks using an activated sludge inoculum.
ATMOSPHERIC FATE: According to a model of gas/particle partitioning of semivolatile organic compounds in the atmosphere, methyl methacrylate, which has a vapor pressure of 38.5 mm Hg at 25 deg C, is expected to exist solely as a vapor in the ambient atmosphere. Vapor-phase methyl methacrylate is degraded in the atmosphere by reaction with photochemically-produced hydroxyl radicals; the half-life for this reaction in air is estimated to be 7.4 hours from its rate constant of 5.2X10-11 cu cm/molecule-sec at 25 deg C. The rate constant for the reaction of methyl methacrylate with ozone is 1.1X10-17 cu cm/mole-sec, corresponding to a half-life of 1 day at an atmospheric concentration of 7X10+11 molecules/cu cm. Because methyl methacrylate does not absorb light in the environmental spectrum above 290 nm, direct photolysis is not expected to occur.
Benzoyl Peroxide:
TERRESTRIAL FATE: Based on a recommended classification scheme, an estimated Koc value of 1,800, determined from an experimental log Kow of 3.46 and a recommended regression-derived equation, indicates that benzoyl peroxide is expected to have low mobility in soil. Volatilization of benzoyl peroxide from moist soil surfaces may be important given an estimated Henry's Law constant of 3.5X10-6 atm-cu m/mole, using a fragment constant estimation method. Benzoyl peroxide is not expected to volatilize from dry soil surfaces based on an estimated vapor pressure of 7.1X10-5 mm Hg, determined from a fragment constant method. In the Japanese MITI test, benzoyl peroxide (present at 100 ppm) reached 84 percent of its theoretical BOD in 21 days, using an activated sludge inoculum.
AQUATIC FATE: Based on a recommended classification scheme, an estimated Koc value of 1,800, determined from an experimental log Kow of 3.46 and a recommended regression-derived equation, indicates that benzoyl peroxide is expected to adsorb to suspended solids and sediment in water. Benzoyl peroxide may volatilize from water surfaces based on an estimated Henry's Law constant of 3.5X10-6 atm-cu m/mole, developed using a fragment constant estimation method. Estimated volatilization half-lives for a model river and model lake are 17 days and 123 days, respectively. According to a classification scheme, an estimated BCF of 250, from an experimental log Kow, suggests that bioconcentration in aquatic organisms is high. In the Japanese MITI test, benzoyl peroxide (present at 100 ppm) reached 84 percent of its theoretical BOD in 21 days, using an activated sludge inoculum.
ATMOSPHERIC FATE: According to a model of gas/particle partitioning of semivolatile organic compounds in the atmosphere, benzoyl peroxide, which has an estimated vapor pressure of 7.1X10-5 mm Hg at 25 deg C, will exist in both the vapor and particulate phases in the ambient atmosphere. Vapor-phase benzoyl peroxide is degraded in the atmosphere by reaction with photochemically-produced hydroxyl radicals; the half-life for this reaction in air is estimated to be about 4.5 days. Particulate-phase benzoyl peroxide may be physical y removed from the air by wet and dry deposition. The maximum absorption of benzoyl peroxide, dissolved in dioxane was 275 nm, with no absorption reported above 320 nm(4), suggesting that benzoyl peroxide may directly photolyze since it has some absorption above 290 nm (sunlight)
Biodegradability: The biodegradation rate for methyl methacrylate at 75 ppm starting concentration,
treated using a mixed microbial population immobilized in calcium alginate gel, was 9.3
ppm/hr; this corresponded to 89% removal due to biodegradation. In the Japanese MITI
test, benzoyl peroxide (present at 100 ppm) reached 84 percent of its theoretical BOD in
21 days, using an activated sludge inoculum.
Integra Adhesives Inc.,
September 3, 2010
Adhesive Kits
Bioconcentration: Methyl methacrylate is not expected to bioaccumulate. Bioconcentration of benzoyl
peroxide in aquatic organisms is expected to be high.
13. Disposal Considerations
Review federal, provincial or state, and local government requirements prior to disposal. Store material for disposal as indicated in Storage Conditions. Disposal by controlled incineration may be acceptable.
14. Transport Information
Transport Canada (TDG):
Adhesives, Class 3, UN 1133, PG III, (When labeled for retail trade, may be classified
as "Consumer Commodity")
US DOT (CFR49):
Adhesives, Class 3, UN 1133, PG III, (When labeled for retail trade, may be classified
as "Consumer Commodity, ORMD)
International Air Transport Association (IATA): Adhesives, Class 3, UN 1133, PG III
(When labeled for retail trade, may be classified as "Consumer Commodity, Class 9, ID 8000")
International Maritime: (IMDG):
Adhesives, Class 3, UN 1133, PG III
Limited Quantity
EmS No F-E, S-D, Stowage Category "A"
Flash Point = 9oC
Note: Despite a flash point of 9° CC, this product has been assigned to Packing Group III as per the
requirements of TDG, Part 2.19(3) and 49 CFR § 173.121 (b).
15. Regulatory Information
CANADIAN FEDERAL REGULATIONS:
CEPA, DOMESTIC SUBSTANCES LIST: All ingredients are listed
WHMIS CLASSIFICATION:
Part A: B2, D2B, F
UNITED STATES – FEDERAL REGULATIONS:
TOXIC SUBSTANCES CONTROL ACT (TSCA): All components are listed in the inventory.
OSHA, 29 CFR 1910, Subpart Z: Meets the criteria for a hazardous substance.
CERCLA, 40 CFR 302: No ingredients listed
SARA 302, 40 CFR 355: No ingredients are listed.
SARA 313, 40 CFR 372: Subject to reporting requirements:Benzoyl peroxide, Methyl methacrylate
SARA 311/312, 40 CFR 370: Immediate (Acute) Health, Delayed (Chronic) Health.
Proposition 65, California Safe Drinking Water and Toxicity Enforcement Act of 1986: No ingredients
appear on the list of Carcinogens or Reproductive Toxins as published on the effective date of this Safety
Data Sheet.
Integra Adhesives Inc.,
September 3, 2010
Adhesive Kits
16. Other Information
Original Preparation Date: September 3, 2010
Prepared by: Kel-Ex Agencies Ltd., 319 Lynn Avenue, North Vancouver, B.C. V7J 2C4
Disclaimer: This Safety Data Sheet was prepared using information provided by
CCINFO. The information in the Safety Data Sheet is offered for your consideration and guidance when
exposed to this product. Integra Adhesives Inc., expressly disclaims all expressed or implied warranties and
assumes no responsibilities for the accuracy or completeness of the data contained herein. The data in this
SDS does not apply to use with any other product or in any other process.
This Safety Data Sheet may not be changed, or altered in any way without the expressed knowledge
and permission of Integra Adhesives Inc.
Revisions: None
Integra Adhesives Inc.,
September 3, 2010
Source: http://www.meganite.ca/uploads/20130510022710110.pdf
Universidad Autónoma de Guerrero. Educación Media Superior Plan de Estudios Universidad Autónoma de Guerrero Comisión General de Reforma Universitaria Educación Media Superior PLAN DE ESTUDIO POR COMPETENCIAS 2010. INGLES III Programa de estudios de Ingles III Universidad Autónoma de Guerrero. Educación Media Superior Plan de Estudios
GLI ABSTRACTS DI ALCUNE PUBBLICAZIONI SCIENTIFICHE RECENSITE NELL'ANNO 2007 DA MEDLINE, LA PIÙ IMPORTANTE BASE DI DATI DELLA LETTERATURA BIOMEDICA MONDIALE. Come si può vedere, la ricerca nel campo dell'agopuntura è molto attiva ed è orientata nei settori più disparati della scienza biomedica. Chi fosse interessato a reperire tutti i lavori